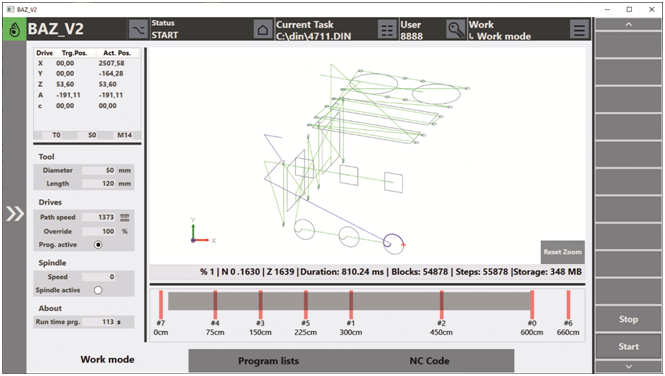
加工中心的触摸式操作界面
无论是铣削、钻孔、切割、精加工、磨削还是珩磨,完整的机加工都需要面向未来的系统解决方案,这些解决方案必须与数字化保持同步,并确保生产技术在高薪国家中的竞争力。
使用CNC加工中心可以节省工业生产中的巨大加工成本,缩短加工时间和生产时间,最重要的是能显著提高加工的准确性和精密度,这些是CNC加工中心取得巨大成功的主要原因。自上世纪70年代初以来,CNC加工中心一直紧跟自动化技术的步伐,如今通过数字化,加工中心被越来越多地集成至灵活的制造集群中。
CNC加工中心的自动化改造需要整体供应商的端到端概念,供应商不仅要掌握各种CNC技术,还要了解加工中心所有技术和工艺的最佳编排,加工中心是整体艺术作品,其潜力无限。
自动化组件相互适配
Ferrocontrol在加工中心的高效自动化改造方面拥有40多年的经验,不仅在棒材加工、窗户生产、开关设备制造和家具行业设立了标准,而且所有自动化组件都相互适配,并针对集成系统解决方案进行了设计:
● 可扩展的工业PC和触摸屏;
● 带CAD/CAM系统和生产计划软件、用于加工中心的HMI软件包;
● 用于CNC、PLC和运动控制的控制器,最多32个CNC轴;
● 多通道,最多可达8个CNC通道,例如使用两个刀具同时加工;
● 总共可多达64个轴,运动轴和CNC轴可自由组合,可扩展的I/O系统以及满足严格实时要求的Ethercat;
● 集成安全功能高达SIL 3,
● 伺服驱动控制器和电机,包括高动态主轴驱动器;
● 动能回收系统(KERS),可实现传动系统的高能效,
● 全集成的机器视觉解决方案,
● 强大的机器管理系统,可用于多个处理中心的数字联网,例如通过OPC-UA或MQTT。
通用的现场总线协议可用于Ethercat和CAN-open的通信,PLC和安全应用程序的程序创建是在Codesys作为开发环境完成的,它可以基于对象高效设计应用程序,并兼顾IEC61131-3等国际标准。
借助基于对象的编程(带有继承、封装和再利用)可以减少工程、测试和软件维护的工作量,这对于具有多个变量的机器特别有利。针对加工中心的所有标准功能,机器开发人员都可以轻松使用预定周期、久经考验的PLC套件,从而加快工程设计并减少测试工作量,轴的配置、参数设置和优化也有专业工具可供使用,从而能够实现快速安全的调试。
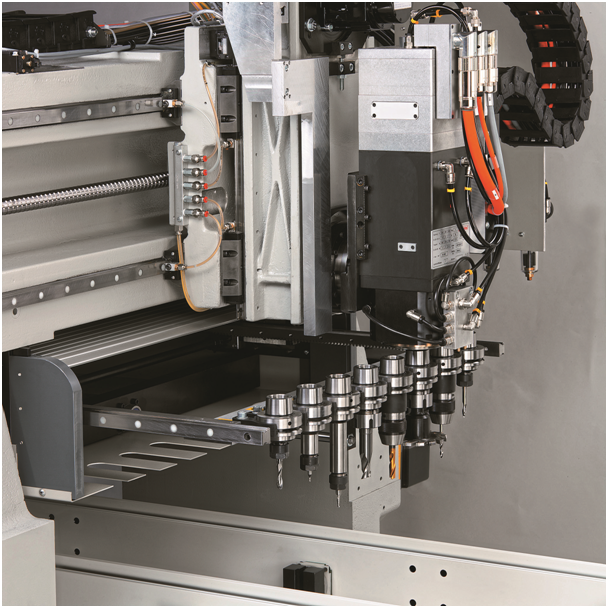
图1 带主轴驱动的5轴加工中心的典型系统架构
应用团队从概念到系列全程协助
Ferrocontrol将其产品和效率视作面向机器制造商的服务,一站式提供一切,这意味着CNC应用团队在对机器方案进行项目规划时就已经开始帮助机器制造商了,随后系列机器的自动化解决方案以交钥匙组件和成品控制柜包括电缆组的方式及时交付,并针对各种应用进行配置和预设参数,例如Ferrocontrol的工业PC,它具有包含客户软件在内的个性化特点,由于机身安装便捷,可以立即使用。
从样机调试辅助到第二级支持的全方位服务为机器制造商提供了长期创新合作伙伴关系的安全性,与国际领先企业在铝、金属、木材、塑料、复合材料、玻璃和陶瓷等加工中心领域的长期合作也证明了这点。
加工中心如今必须做什么?人们知道的加工中心不过是由CNC控制的机床,配备刀库和换刀装置,以便能够使用多个切削刀具。
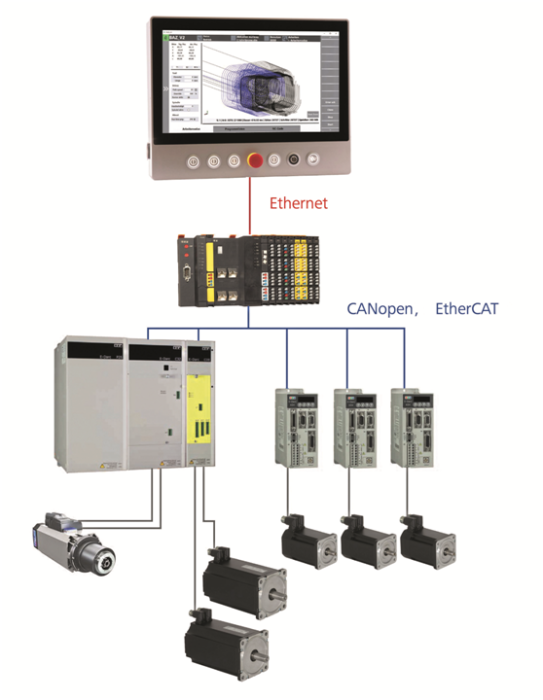
图2 加工中心的刀库示例
如今的加工中心通常还配备自动工件更换器,通过一次装夹就可以加工所有工件,一次装夹时通常会用到各种加工过程,包括钻孔、攻丝、铣削、切削和磨削。
还可以加入其它过程,例如激光打标或激光硬化。通过一次装夹加工复杂工件具有以下优点:周期时间短、无需改装、夹紧装置少,最重要的是由于无需重新夹紧工件,重复精度更高,结果提高了质量并降低了制造成本。
更加高效地操作高速主轴
每个CNC加工中心的核心都是移动工具主轴,主轴电机通常还是通过变频器供电:但如果不需要工具上的扭矩,这种方式就会导致大量不必要的热量损失,这样不仅效率低,而且还会缩短主轴驱动器的寿命。
因此应在整个转速范围内更好地控制刀具主轴,这样就只有实际需要的能量进入电动机,Ferrocontrol生产的、基于FPGA的(现场可编程门阵列)伺服驱动系统E-Darc C可以帮助控制同步和异步主轴电机,转速最高可达20000 min–1,这样刀具主轴可在磨损极少且节能的情况下运行,负载跳跃引起的转速偏差也会自动纠正,工件厚度和进给速度的变化对加工质量基本没有影响。高频主轴的控制运行会使工件表面的整体质量更高,同时最大程度地减少后期处理的手动工作量。
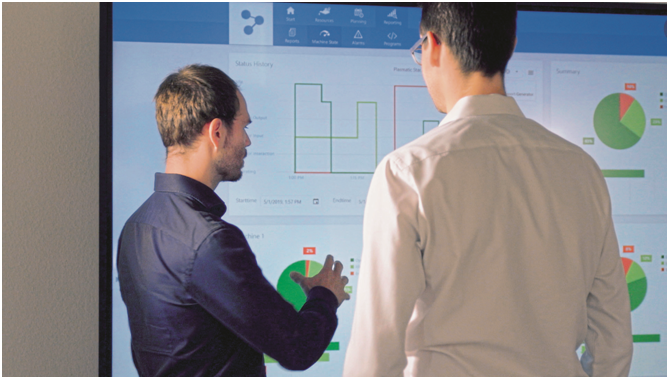
图3 机器管理系统作为加工中心的数字化扩展
加工中心有一个自动换刀系统,用于快速更换主轴上的从动刀具,刀具保存在刀库中,换刀将“切屑到切屑时间”降至最低,现代化CNC加工中心的这一时间不到2秒。
即使是包含许多单独加工步骤的复杂加工周期也可以在较短的周期时间内完成,HMI为操作员提供了优化周期的专业工具,借助基于CNC的实际运行时间计算功能,不仅能够精确预测加工时间,而且还可将这一信息用于可靠计算加工成本。使用机器管理系统可以更加方便地解决这些任务,该系统具有针对车间数字化的多种功能以及一个CNC应用程序的数码双胞胎。
换刀还为驱动技术提供了令人感兴趣的优化潜力,例如智能参数集管理非常实用:最多可以存储16个与工具相关的参数集,这些参数集还描述了工具的几何形状,这样更换工具时能够快速切换参数集。
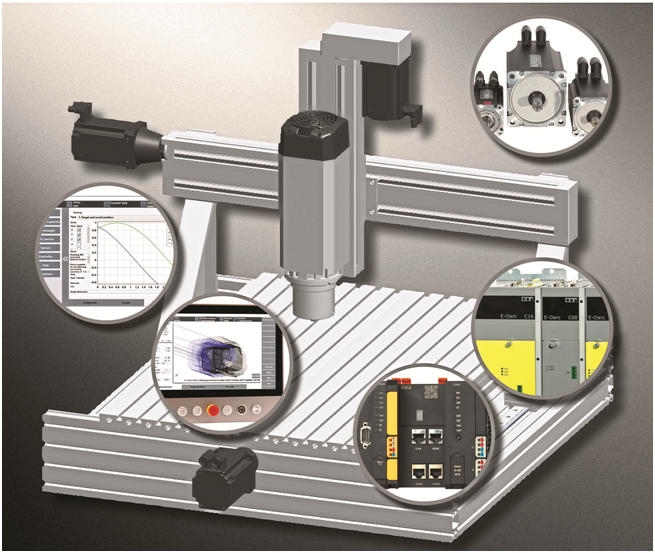
图4 CNC加工中心的自动化解决方案包括驱动和控制技术、配备BAZ-HMI包的平板电脑以及工程工具
由于工具(例如锯片、丝锥、钻头或铣刀)的大小和形状不同,有必要存储和选择与工具相关的参数集,这样每个工具的驱动控制都能获得最佳的控制器参数,实现高动态和低能耗。借助集成的参数集切换,机床的出色装备可缩短换刀时间即切屑到切屑的时间,此外使用加工中心时,高效运行必需的各种处理任务通常必须自动完成,因此Ferrocontrol的加工中心控制系统还具有各种针对更换工作台或托盘系统的功能,以便进行平行装卸,这样在加工工件的同时能够准备下一个工件。
全自动化和数字化
无论是3轴还是5轴同时加工,对要求高的CNC加工中心进行自动化改造都需要一整套CNC功能。借助Ferrocontrol为加工中心提供的CNC解决方案,机床制造商可以获得经过多次实践检验的完整模块化系统,其中所有组件和功能都进行了最佳适配,从控制和驱动技术到针对加工中心的、带有触摸优化的HMI表面的平板电脑,再到可以无缝集成至自动化系统中的安全解决方案。
评论
加载更多