在应对金属枢轴销全自动内外部检测的挑战中,Innovision挺身而出,与客户制订了一个计划。Innovision与其姊妹公司——设备制造商Sampas共同开发出一个紧凑型测试系统的整体方案,它分为2个步骤,由3个机器人、1个旋转分度台和进出料生产线组成。
不过对于这项繁琐且高度复杂的检测任务而言,该方案依然不够完美,于是Innovision的图像处理器和视觉初创公司HD Vision Systems结合到了一起。Innovision的设备开发项目经理Kim Henrich概括了当时的情况:“枢轴销的内外部检测确实是一个非常艰巨的挑战,此前这项任务一直由制造商的员工完成,采用工业图像处理的首次尝试以失败告终,因为设备不仅应具有很高的检测频次,还要可靠识别轴销内外部的所有缺陷。”后者应该达到100%的准确率。
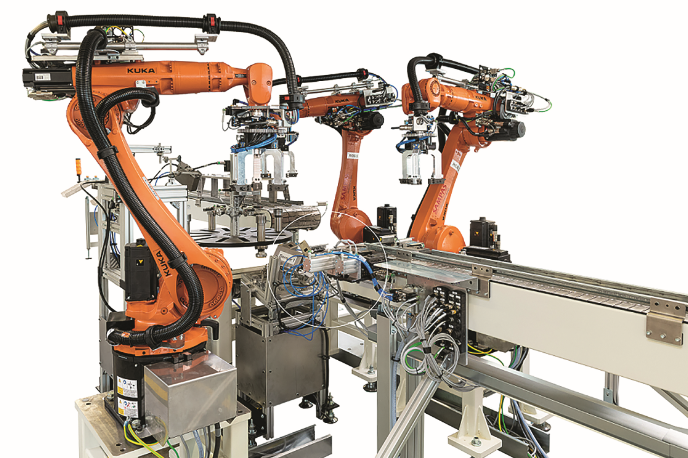
图1 全自动检测金属部件
艰难的图像检测
有金属光泽、部分涂抹着油的轴和枢轴销使图像检测很难顺利完成,此外判定轴销合格、不合格或需返工的全部检测必须在3.6 s内完成,因此Innovision决定在项目中使用新技术来扩展自己的专业能力。HD Vision Systems的基于光场的传感器Lumi Scan X取代了最初计划的3D传感器,凭借这一技术方法,紧凑的3D多摄像头阵列对眩光更加稳定,减少了遮挡,只需一次拍摄即可提供精确的深度信息。“由于采用了光场方法,我们的Lumi Scan X传感器与传统3D传感器的工作方式不同,因为光场描绘了所有光信息的整体数据,除了亮度、颜色和来源外,还包括光的方向,采用多摄像头阵列显示,光场减少了三维场景中的反射和遮挡。”HD Vision Systems的创始人Christoph Garbe博士介绍说。
这样一来Innovision的项目管理能够将枢轴销的检测分为3个步骤。
(1)进行内部检测时,两台工业机器人将枢轴销展示给安装在下方的光场传感器,并两次将其旋转120°,HD Vision Systems的软件使用这些数据在几秒钟内完成基于KI的缺陷检测。
(2)接下来工业机器人将轴销放在旋转分度台上,在这里另一个传感器根据规定标准检测轴销的外部。
(3)最后第三台机器人根据相应检测结果将枢轴销分送至由三部分组成的输送带的相应轨道上。合格零件沿生产线继续向前走,不合格零件这时可以再次加工或熔化,通过这种方式,使用它们的汽车制造商可以避免错误供货造成的昂贵费用。
使用Lumiscan X光场传感器很快解决了轴销的外部检测问题,它背后的技术成功减少了金属光泽。为了正确检测轴和枢轴销无法统一识别的内部,人们选择使用人工智能,在人工智能的帮助下,视觉系统能够学会识别变形、划痕等造成的不一致的错误图像。
为了让AI图像处理做出绝对准确的判断,系统需要进行训练,因为人工智能算法(在这种情况下是深度学习和神经网络)不能使用固定参数,取而代之的是,人工智能系统开发出独立的决策矩阵,为了调节这些网络,软件需要足够的测试材料和训练单元,人们很快就发现,所选择的解决方案大有前景,但要达到100%的检测可靠性,还需要更多有缺陷的零件。在多次实验中,Innovision和HD Vision Systems 的团队收集了有缺陷的枢轴销图像,挑战在于针对每种缺陷获得足够多的残次品,随后的软件训练能够在每个中间步骤之后改善结果。
该系统可识别各类缺陷
今年年初大功告成:在测试运行中,系统能够正确识别包括内外部检测在内的各类缺陷。汽车行业供应商现已开始使用这一系统,预计整个系统将在两年内收回全部投资。
“枢轴销的检测本身确实是一项重要的任务,我们为自己的成就感到自豪,同时很高兴能够在与Sampas和HD Vision Systems共同组建的团队中为我们的客户开发出一个好的解决方案,联合起来我们确实是最强大的。”Henrich总结道。
评论
加载更多