在MM《现代制造》主办的以“问道数字化 智造竞争力”为主题的“第十六届MM现代制造·新自动化论坛”上,台达集团机电事业群智能制造事业部营销总监杨应龙做了题为“台达智造实践与电子行业智能产线升级”的演讲,他针对制造业的挑战与需求,畅谈了台达智能制造的实践,结合智能产线设计概念提出了电子组装智能升级路径,并分享了智能产线设计实例。
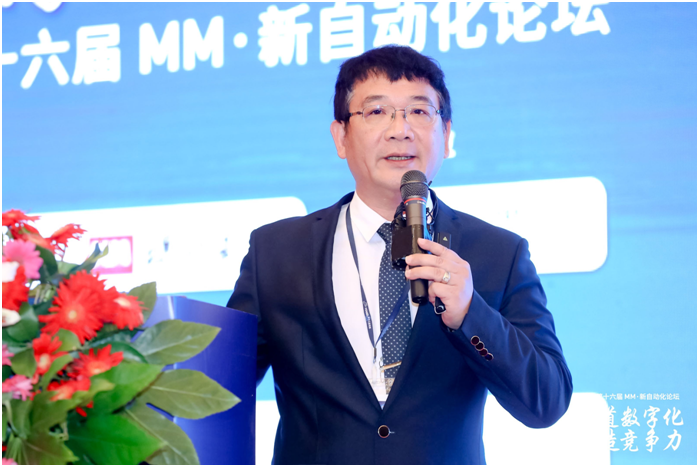
台达集团机电事业群智能制造事业部营销总监杨应龙
当前,制造业面临越来越复杂的挑战,除了大环境的气候变迁、人们消费习惯的改变、高龄化社会的来临、AI技术的应用推广,还有贸易摩擦升级及全球新冠疫情等国际局势的风云变幻。同时,制造业自身存在着少量多样生产、绿色环保节能、产品生命周期缩短、工资上涨与工人短缺并存、低成本高质量等诸多难题,消费电子产品领域尤其如此。
杨应龙指出,制造业如何在人力短缺的疫情时期,仍能维持企业的运作效能呢?唯有智能制造是重要解方,以智慧化降低对人力的依赖,才能持续维持竞争力。
自1971创立,台达已经在电源和直流风扇产品制造领域成为世界第一,台达生产的PLC和变频器等产品也通过灵活、快速的智能生产成功稳固了市场的领导地位,并一直在不断推进工厂转型,自2015年开始,台达向智能制造方向持续精进发展,建立了IT与OT融合的智能制造生产体系。
在针对生产作业进行简单化、合理化、标准化的改善之后,近几年台达已对产线的自动化投入了大量的资源。基本上,台达的每一类产品,都打造出一条高度自动化的示范线,以精简人力,减少了因人而造成的变异,使得产能与加工获得明显的改善。同时,为了实现自动化生产,台达在产品设计之初,针对自动化设计(DFA)就设定了标准的准则。另外,除了自动化以外,台达也导入各项生产执行营运管理系统,对于工厂的人、机、料、法,做到了严密而实时的监控与管理。同时,通过机联网,使得底层的生产信息向上传达到MES,台达已经实现了产线各项信息的可视化,以及智能换线功能。杨应龙表示,台达开发的转文件程序以及大数据分析技术,已经在内部基本实现了信息自动化以及工厂的智能化,当然,台达还会持续不断地精进下去。
从工业机器人到智慧设备,为客户打造完整自动化系统及智能产线,是台达最重要的智能制造实践。据悉,台达在吴江三厂的可编程逻辑控制器 (PLC) 示范线已经达到突出的效果:产能大幅提升,实现了直接人均产值提升3-5倍、产能提升70%、生产使用面积降低35%的智造效益。目前台达PLC智能制造示范产线可弹性生产多达138种产品类别,对应5种不同工单类型,每日可换线15次以上。示范线进一步实现数据分析管理、能源管理、质量诊断、串联客户订单及厂务监控管理系统迈向整厂智能化。
在台达对智能制造产线的设计理念中,已经形成了对电子制造业的标准设备规划和定制化,智能工厂的核心枢纽必须充分运用数字化规范全厂的作业流程,包括:对生产现场进行全制程的管控,建立起生产流程的标准作业规范,实时核查制程中人、机、料、法、环、测信息,防范错误;精准追踪生产进度,提高生产效能与质量良率,落实产品履历追溯。此外,制造可视化管理系统必不可少。杨应龙强调指出,一个企业要推动智能制造,必须从上至下地贯彻,才能建立起完整的智能制造体系。
改善无止境,台达致力于打造全方位智能工厂标杆,除了提供完善的系统产品,如自动化设备、可视化机联网、制造执行系统、能源管理厂务监控等,还全面提供卓越的一站式服务,包括咨询顾问、诊断服务及整合设计、智能制造整体方案执行、持续升级建议与方案。
评论 0
正在获取数据......