水泥工业属于传统制造业,当前的发展模式比较粗放,具有能耗高、资源利用率低、生产效率低、环境负荷重等特点。对此,安徽海螺集团有限责任公司围绕水泥生产核心业务及水泥制造流程型生产的特点,利用自身长期生产经营过程中积累的生产制造、设备运维和经营管理知识,基于移动通信网络、数据传感监测、信息交互集成及自适应控制等关键技术,创新应用了数字化矿山管理系统、专家自动操作系统和智能质量控制系统等涵盖水泥生产全过程的智能化控制及管理系统,实现了工厂运行自动化、管理可视化、故障预控化、全要素协同化和决策智慧化,形成了“以智能生产为核心”“以运行维护做保障”“以智慧管理促经营”的水泥生产智能化模式,为传统产业的转型升级和高质量发展起到了良好的示范引领作用。
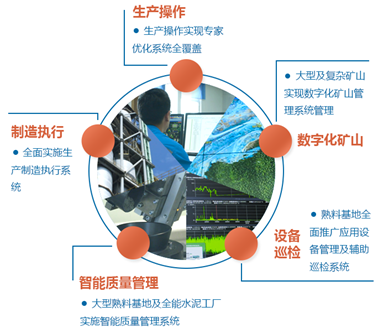
图1.海螺集团智能工厂战略规划
实施路径
一、建设基于水泥制造知识库的智能生产平台。建立水泥制造全过程知识库,构建包含数字化矿山管理、专家自动操作和智能质量控制三大系统的智能生产平台,将工艺机理特性、装置运行数据和专家操作经验等深度融合,让积累的生产知识、管理经验软件化,实现知识传承,最终达到降低人员劳动强度、提高产品质量和降低资源能源消耗的目标。
二、构建水泥生产支撑保障的智能运维体系。突出“稳产助优产、优产促节能、节能优环保”的生产理念,建设包含设备管理及辅助巡检、能源管理和安全环保三大系统的智能运维平台,实现原料磨、预热器、回转窑、篦冷机、水泥磨等核心装备及辅机设备的在线监管、重大故障提前预判,实现全厂能源消耗和安全环保的集中与区域管控,为智能生产平台提供高效、安全、节能、环保的运行环境;采用信息化手段减少高、偏、远等高安全风险区域人员介入强度,使人员作业轨迹可查询,人员、设备、环境安全隐患可预警,促进设备长周期、高效运行,有效降低生产经营风险。
三、打造水泥生产销售的新模式。利用云计算、物联网、大数据等信息通信技术,将水泥传统生产、销售模式与互联网融合,建设包含制造执行系统和营销物流管理系统的智慧管理平台,将生产原料消耗、能源消耗、备品备件消耗等生产数据与供、销、财、物等业务数据互联互通,打通了从市场到工厂、从需求到产销的水泥生产全流程的数据流、信息流,实现了水泥工厂订单、计划、生产、发运、销售、服务整个过程的信息化,有效优化了生产组织体系和销售服务流程,大幅提升了客户体验。
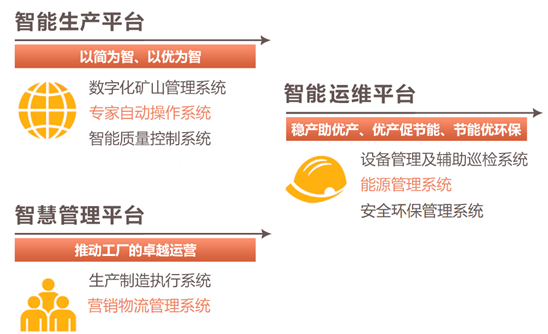
图2.水泥智能工厂三大平台
实施成效
海螺集团水泥智能工厂实施后,生产线设备自动化控制率达100%、生产效率提升21%、资源综合利用率提升5%,能源消耗下降1.2%,质量稳定性提升3.7%,工厂主要经济技术指标得到持续优化,员工劳动强度得到有效减轻,取得了良好的经济及社会效益。2019年,入选国家智能制造标杆企业。
评论
加载更多