10余年前,采用砂浆的切片技术在单根晶棒上可以切出1000片左右,今天,采用金刚线的切片技术可以使得这个数字发展到高达4000-5000片,并且,一根晶棒的切割时间也从过去的十几个小时缩短到90分钟,这一切都意味着,仅在切片这一环节,光伏组件的成本就获得了大幅度的下降。然而,这种效率的大幅提升同时也意味着控制系统更高精度与相应能力要求。
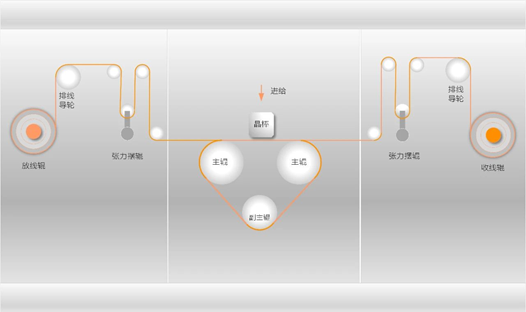
图1-多线切割基本原理图
通过放卷张力控制、经过多个辊(双或三主辊)的排线、棒料的进给、收卷,并且通过金刚线的往复实现切割,以提高金刚线的利用率。整个金刚线切片系统要达到非常高精度、稳定的张力控制,机器才能确保切割的稳定,高效,达到高品质的生产,并较之以往的浆料切片更高的产出。
为了降低成本,大尺寸、薄片是未来的发展方向,对于金刚线的切割而言,更细的金刚线才能切出更多的片,并降低表面粗糙度,进而更好的成片质量,而对于线速度而言,则意味着更大产能带来的成本下降,但这都对控制系统包括恒张力控制、高精度排线、高精度进给等提出了更高的要求。
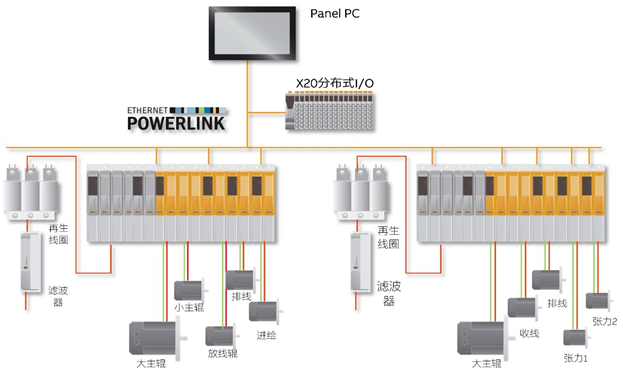
图2-贝加莱光伏切片系统解决方案硬件架构
图2是贝加莱为多线切割系统提供的解决方案,ACOPOSmulti提供了共直流母线驱动技术,通过POWERLINK实时以太网提供百微秒级的高精度同步。
切片系统的功能性设计
在晶棒拉制后,经过切方,进入多线切割,这是至关重要的一环,每个晶棒都价值不菲,如果不能高品质的生产出产品,那就会成为“成本”的构成,随着金刚线变得更细,这也使得对于切片的过程控制更为“精细”的要求,切片过程必须能够控制非常精准,且同步精度高,才能确保晶片裁切过程的高品质,整体的方差最小。

图3-多线切割系统的功能需求
张力控制技术
卷径与张力是贝加莱控制系统的基本工艺控制模块,借助于在印刷、塑料、包装众多领域数十年的积累,对于各种张力场景的张力控制贝加莱均可应对自如,自动排线、平台控制、掉电停车功能是多线切割行业所特殊的需求,贝加莱为此专门进行了大量的测试验证,成熟的技术确保了拿来即用。
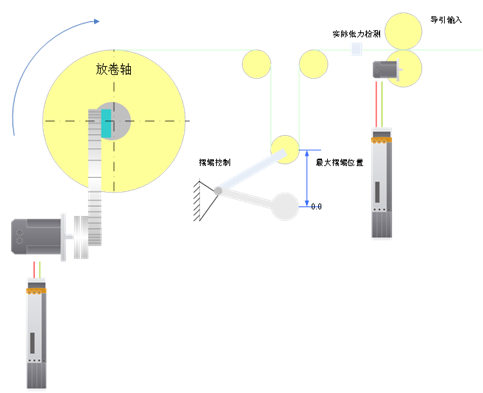
图4-基本的张力控制模型
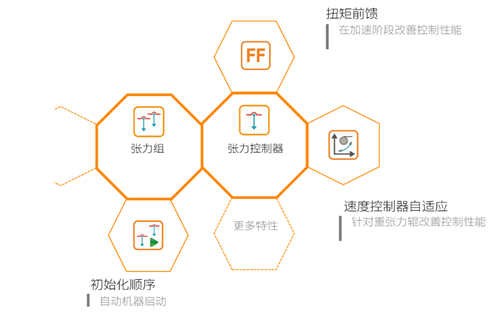
图5-贝加莱张力控制的特点
对于贝加莱的张力控制来说,可以实现扭矩前馈,这确保了在加减速阶段也可以实现稳定的张力控制,不仅对于光伏金刚线,对于其它材料的张力控制同样如此,因为,这可以大幅降低开机浪费,通常在生产中被认为是必然的。另外张力的自适应、多组张力的解耦等,都是贝加莱张力控制领先的技术特性。
自动排线
由于金刚线经过主和从辊必须要排线,而辊子是加工辊、主/从辊的排列使得在整个排线过程中,特别是在加减速过程和排线换向过程中,其张力处于一种变化的状态,因此,需要高精度电子凸轮曲线轮廓,高阶曲线来实现更高的精度控制,这对于机器来说,只有如此,才能确保排线精度高,切片的单片均方差最小。
主辊控制
切割室主辊,在绕线和切割过程时,可以在线实现电流环和位置环模式切换,电流同步可以保证两个主辊出力同步,有效的保证切割区内的金刚线张力稳定,同时也能很好的保证切割线弓最小,切割力最大,以获得更高的切片质量。
审计追踪
mappAudit是贝加莱系统中的mapp功能组件,它为系统提供了审计追踪能力,从生产的可追溯性角度,生产需要了解谁在什么时间做了什么,并对其进行记录,以不可篡改的形式保存数据,这样就确保质量、工艺的可追溯性,以为生产工艺人员的质量调整与优化带来数据依据。
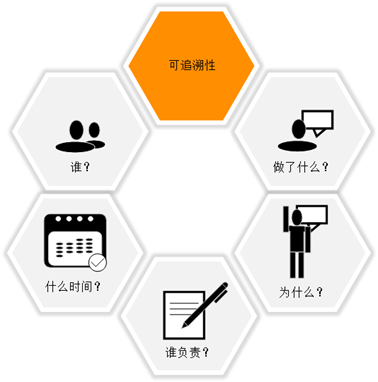
图6-审计追踪原理
对于光伏晶片制造商而言,审计追踪是提升其工艺质量管控水平的关键,系统具有该项功能,将会使得这一实现变得简单,来自于在制药领域的mappAudit功能,贝加莱同样将其可用于光伏晶片生产的追溯。
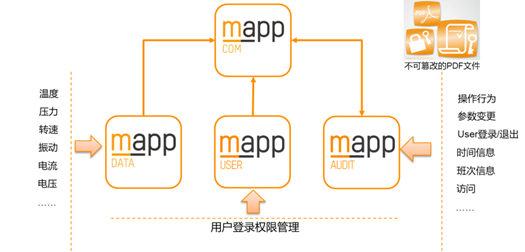
图7-通过mapp模块组合实现审计追踪与数据应用
在审计追踪的管理中,机器的各种参数以mappData模块进行收集应用,并通过mappUser的用户管理,以及mappAudit的审计追踪模块对其进行记录,通过mappCom来实现软件之间的连接。
掉电停车功能
对于光伏切片而言,突然掉电情况下的同步停车是非常必要的,否则,对于生产的浪费是巨大的,除了金刚线晶棒材料的损失,再恢复机器所需的成本也是高昂的,因此,掉电停车功能对于光伏切片是必选项。
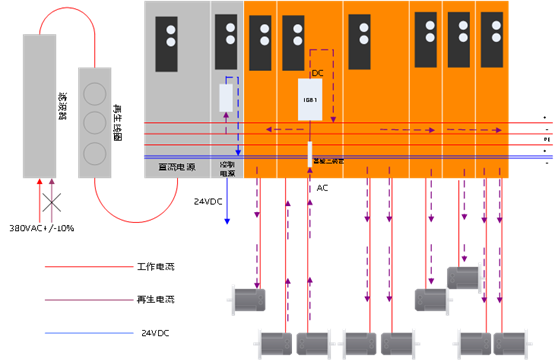
图8-基于ACOPOSmulti的掉电停车功能
采用ACOPOSmulti共直流母线驱动技术,当系统主轴在制动时产生的电流通过再生线圈回到直流母线,并经过DC/AC转换,提供给其它轴的同步停车。
数据驱动的预测性维护技术
将硅棒切割成厚薄均匀、切壁光滑的硅片,依赖于多线切割机的稳定运行。但在实际的生产中,难免会有设备出现故障的情况。在切割状态下,设备的突发故障导致的突然停机,对于昂贵的硅棒会造成不可修复的损伤,导致直接报废。这样的突发停机带来的材料损失及停机检修的停产损失等是巨大的。对于机器高速运行而言,其主辊和线辊的轴承承受较大的考验,并且也是对机器影响最大的关键部件,因此,如何能够在故障发生之前就对其健康状态进行预警,使得工程师们能够在工作间隙对设备进行及时的干预、维修,就成为了避免经济损失、保障生产的关键。
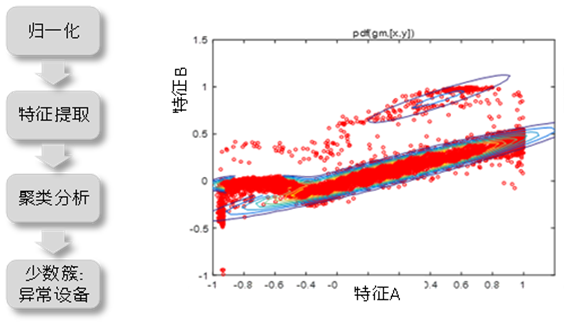
图9-基于聚类分析的预测性维护
如图9所示,基于多年积累的行业专家知识,首先对多台设备的数据进行恰当的特征提取,以提炼出数据中与设备健康状况最相关的信息。之后,使用人工智能算法对数据进行自动聚类,使得特征相似的数据聚成一簇,而不相似的数据聚类成不同的簇。可以很自然的推断,在多台相似类型的设备中,大部分设备是健康的,数据特征是类似的。所以,聚类结果中有着大量样本点的簇可以视为健康簇。而那些游离于健康簇之外的样本、少量点组成的小簇,则指征着设备的异常工作状态。
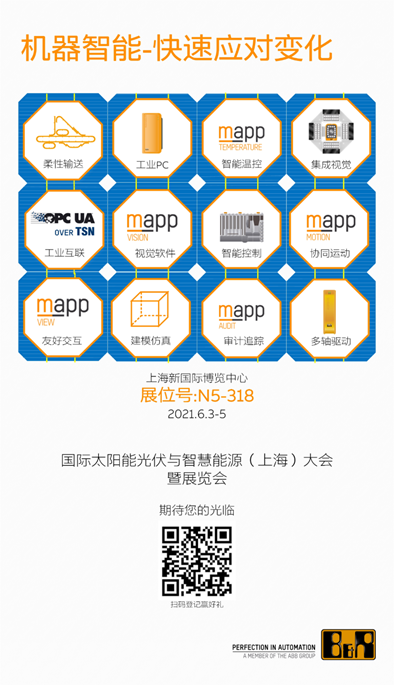
评论
加载更多