方案名称:复合机器人数控CNC上下料应用
供应商:节卡机器人股份有限公司
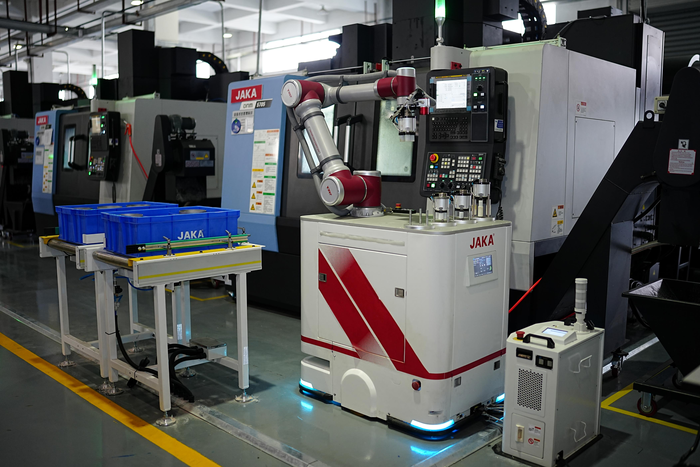
方案描述
一、方案基本情况:
CNC数控加工在现代制造业中占有核心地位。尽管我国机床数量全球领先,达到800万台,但其中一半已运行超过10年。同时,机床上下料主要依赖人工或专用设备,存在生产效率低、质量不稳及安全的风险。虽然众多企业积极探索自动化上下料的解决方案,但均未实现产业化,难以满足高质量和大规模生产的需求。因此,亟需寻找高效且安全的自动化上下料解决方案,以提升制造业水平和促进其快速发展。
为解决行业痛点,节卡推出了市场首款专为CNC加工环境而设计的复合机器人。该产品集成了AGV移动平台(脚)、协作机器人(手)和视觉系统(眼),利用机器视觉、机器学习和自适应控制等技术,实现“手、脚、眼、脑”的智能协作。同时,该机器人支持多种通讯协议,能无缝对接现有CNC机床,无需大规模改造。能有效管理数十甚至上百台机床,显著减少成本,提高生产灵活性。最重要的是,该产品已成功商业化,成为行业应用标杆。
二、方案亮点、优势及案例情况:
(一)行业痛点
统计数据揭示,在一个完整的生产周期里,机床的加工时间只占总时间的5%,而高达95%的时间被用于物流环节。这导致物流成本占据整体成本的40%。因此,当对CNC机床进行自动化改进时,关键在于优化物料的转运效率。目前,改造主要面临如下需求痛点:
1)环境要求高:传统自动化设备通常仅具有IP54的防水等级,只能抵御液体飞溅。在面对机床内部的切削液飞溅、粉尘、油污和高温环境时,难以长久稳定工作。
2)空间限制:工作场地通常狭窄,宽度仅为1.0-1.5m,只能容纳手推车。而传统自动化设备需要固定安装,进一步降低了通道空间。
3)物料多样性:加工物料种类众多,规格复杂。同时,机床的工作区域仅为600x600x500mm,这增加了设备在上下料过程中的碰撞风险。
4)高成本:数据显示,传统自动化改造通常需要设备与机床一一对应,导致改造成本增加。
(二)方案难点
为解决上述需求痛点,众多企业都推出了各种解决方案。然而,受到现场环境复杂性的影响,多数产品仍停留在概念验证阶段。因此,尽管机床自动化改造受到广泛关注,成功商业化的案例却相当少见。此外,上述方案主要是为特殊场景定制的,商业推广面临困难。
自动化改造实施难点:
(1)安全协作。由于设备需要与人类进行高度协作,如果安全措施不足,可能会对人员造成伤害或危险。因此,需要在设备的设计和应用中加强安全措施,确保设备与人类的安全协作。
(2)精度标准:CNC设备作业中需具备秒级的时间精度和微米级的位置精度。因此对物料上下料定位精度和稳定性有极高要求,通常需要做到1mm以下。
(3)环境适应性:设备应能在含切削液、碎屑或不稳定光照的环境中正常运行,需具备防水、防尘和视觉识别功能。
(4)部署灵活性:考虑到工厂内复杂的机床布局,自动化设备需要具有便捷的操作方式以及高度的移动性,以便快速部署和生产。
(5)数据交互:由于设备和机床系统异构,数据通信存在困难。因此,需要建立统一的数据交互机制以确保顺畅运行。
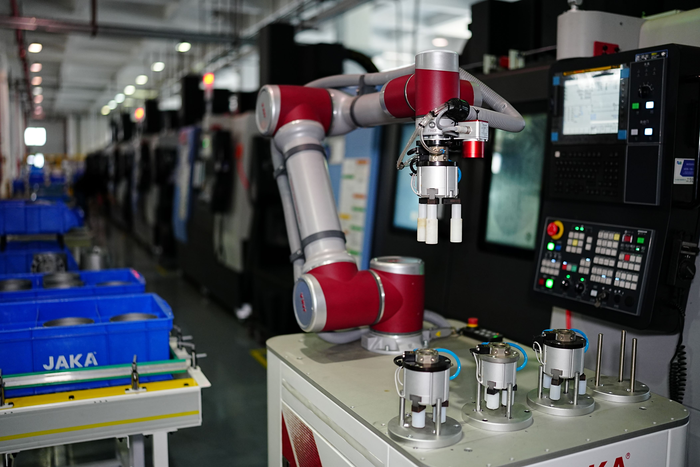
(三)解决方案
针对应用难点,节卡设计了专为金属加工场景设计的复合机器人:
首先将应用的难点细分为工作性能、作业能力、续航能力和易用性四个维度,并分别设定量化标准。工作性能方面,机器人需达到IP68的防水等级、重复精度达到±0.03mm;作业能力方面,目标是使单个机器人能够管理多达几十台甚至上百台的设备;续航能力方面,机器人需满足24小时的连续生产要求;易用性方面,机器人应具备快速部署的能力。接着,根据上述量化指标,进行机器人的设计。利用运动学、动力学和控制理论等技术完成机器人的运动规划和路径规划;考虑光照、物体形状、颜色、表面纹理等多个因素,使用机器视觉、深度学习和模式识别等技术完成对工件位置和姿态的识别和检测;综合电路设计、控制电路设计、结构设计等方面,完成机器人样机搭建。
然后,在实际CNC加工环境中测试机器人原型机,识别并解决了现场存在的问题,并对机器人进行改进。最后,进行机器人的规模化生产,形成商业化产品。
同时,节卡对机器人的工作流程进行了深入分析,并成功制定了一套标准化作业流程,以便于规模化应用。具体流程如下:
1)CNC系统发出开始信号,标志着生产新阶段的启动。复合机器人立即对此做出反应,携带物料,自动导航至预定工作区。
2)CNC机床自动开门,机器人启动其自身的视觉系统,精准识别待加工物料,并将其送入CNC机床中。期间,机器人始终与CNC机床进行信号交互,保证加工精度。
3)完成加工任务,机器人将成品从机床中取出,并放置在托盘上,以便后续质检和包装。
4)机器人继续移至下一工作区,准备进行下一个任务。
通过这一系列标准化操作,生产效率得以提升,同时确保了产品质量的稳定性和可靠性,为现代CNC加工提供了有力支持。
(四)技术创新点
1)工作性能:标准场景工作节拍达到20s、具备IP68防护等级确保在机床的恶劣环境下稳定工作。具有±0.3mm的综合定位精度,确保上下料准确,且取放过程实时监控调整零部件受力,有效避免零部件损伤。
2)作业能力:利用激光SLAM技术实现自主导航和路径规划,打破作业范围限制。同时,兼容各种总线协议,实现一台机器人可管理多达数十或上百台机床。
3)续航能力:重新设计了电缆接口和电池充放电系统,将单电池改为双电池,避免了移动机器人充电对作业时长的占用,可实现24小时连续生产,单次换电续航可达5小时以上,可实现自动换电和手动换电,手动换电时长不超过1分钟。
4)易用度:统一了操作系统和人机交互接口,同时延续了节卡的图形化编程方式,极大的降低了产品的使用难度和入门门槛。
三、应用推广情况:
该款复合机器人在精密制造领军企业东山精密成功部署了30多台,主要应用于CNC机床加工。这标志着国内首次在CNC行业的大规模应用,成为制造业升级的首选方案。该技术不仅推动了CNC加工向智能化和自动化的转型,也显示出巨大的市场潜力。除此之外,多家国内外知名企业如广汽发动机、天津丰津等也已采用该产品,进一步加速了行业的高效发展。
文章来源:节卡机器人股份有限公司
图片来源:节卡机器人股份有限公司
转载平台:企业供稿
责任编辑:朱晓裔
审 核 人:李峥
评论
加载更多