无可否认,我们正处于第四次工业革命的关键时刻。最早利用数字化生产的革命者已经从中获得了客观的利益,例如,能效的提高和故障排除的加速,减少了生产过程中的停机时间,提高了资本回报率。然而,人们现在仍然担心,这种数字化能否为现有的员工所接受,或者说,人的经验和知识是否还能延用。
我们如何解决这种矛盾,如何确保数字化能够在整个工业生态系统中得到大规模传播和利用?我们的答案是:赋能于人。
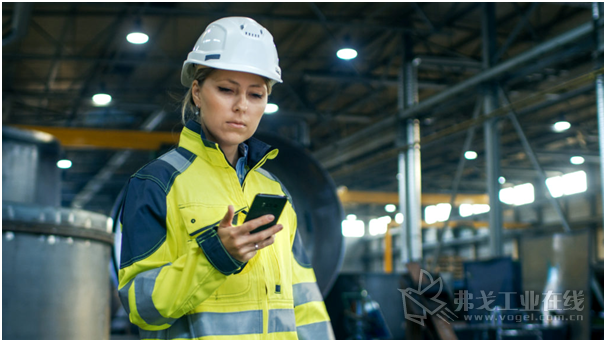
技术让人变得更强大
为运营商提供移动设备、数据分析、增强现实和透明化连接,决策将变得更智能、更快捷,制造商也更好地满足日益严苛的市场需求,实现更灵活且可持续的制造。例如,数据的收集能够推动全新的操作动作与程序。举个例子,资产利用流程数据能够延长相关工业资产的使用寿命,而模拟和场景计划工具,可为原材料和能源供应商的选择提供参考,为最优交付方案等问题提出可持续的解决方案。
在智能工厂中,你不仅仅能看到包括自我学习在内的最新智能技术,还将一睹专业技术操作人员与新技术的无缝合作,实时的操作与管理工厂,提高生产效率。人力因素在数据的收集、比较和分析中不可或缺。
数字化转型要求紧密的连通与协作
促成数字化的因素,包括人与产品、机械的连通,人与人的协作,以及整个产业价值链的协同。如果说数字化的推广与利用存在风险,这种风险就在于企业如何把控数字化进程,如何培训员工迎头赶上,拥抱智能制造给其日常工作带来的变化。
推动创新与适度的技术实施固然重要,但这还不够。人们需要亲身体验创新所带来的好处。在我们企业自身的数字化之旅中,试验、点对点学习和跨站点协作最为有效,这能够确保员工快速接受、推崇和采用新的技术。我们的员工一直在寻找机会学习与利用技术,并从中获益良多,这让他们之间也能够传递知识,了解流程的调整,同时,员工也能更好地预测停机风险。
中国的成功案例
不久前,施耐德电气位于法国的Le Vaudreuil工厂被达沃斯世界经济论坛在其第十二届新领军者年会期间授予全球制造业领域最先进的九大“灯塔工厂”之一。在中国,包括上海、武汉、天津的三家工厂,也在近期荣膺中国的工业和信息化部国家级“绿色工厂”称号。
当前,施耐德电气正在全球范围内积极推进基于面向工业市场的EcoStruxure架构实施的“智慧工厂”项目,该项目将向客户展示施耐德电气智慧工厂的价值,以及数字化转型的最佳实践。施耐德电气的智慧工厂部署了依托EcoStruxure架构与平台的解决方案,以及覆盖互联互通产品,边缘控制,应用、分析与服务三个层面的能效管理与自动化软、硬件产品。
到2018年末,施耐德电气开放了8间可供参观的,基于面向工业市场的EcoStruxure架构的“智慧工厂”(包括2家位于中国的工厂)。目前,施耐德电气在全球约38家工厂(其中8家中国工厂)中,通过部署EcoStruxure™解决方案,使其制造工艺和能源消耗得到了优化,同时,通过使用可视化的管理工具,这些工厂的员工还进一步提高了日常工作的绩效。
施耐德电气在武汉的工厂,是施耐德电气全球“智慧工厂”项目中的示范工厂之一,利用有限的资源实现了高收入增长,这让我们看到推动数字化的必要性:
· 质量问题减少15%
· 能耗降低5%
· 整体设备效率提高4%
这间工厂中人的力量是我们能获取这样成果的核心因素。在这里,机器、工厂、配电和电网方面的专家扮演着数字化推广特使的角色,为数字化的推广与成功应用铺开了道路。他们建立了标准体系结构,囊括所有的优秀实践经验,同时在中国各地进行推广,推动新技术实施、测试和升级的跨站点协作,这些技术包括数字能效管理系统、先进生产调度和COBOT/AGV自动化。
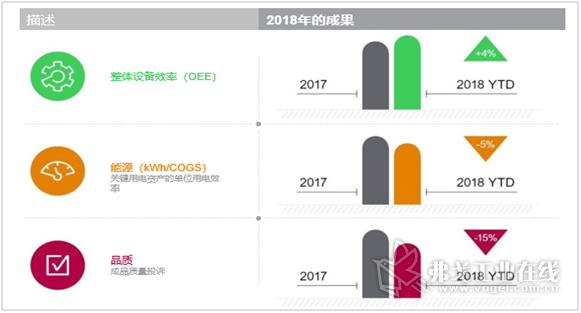
专家在内部培训中发挥着重要作用。他们已经培养了300多名员工,在全区域内肩负起重建、测试与解决实际客户问题的责任。实践经验的分享不仅限于业务的变化上,同时还涉及财务和人力资源等其他部门,以保证整个生态系统都能为未来工厂做好准备。结论是,我们也许认为智能制造更多强调的是互联互通,然而协作能够把企业带到更远的地方。
评论
加载更多