人类通过视觉认知文字、图片和周围环境,机器人要感知和识别工作环境,同样也离不开视觉系统。本文研究并实现了一种工业分拣机器人的视觉定位方法,机器人视觉引导系统借助三维图像处理技术用于定位容器里的零件,软件通过对CAD模型和三维图像的比较,检查给出零件的夹紧位置,以便分拣末端抓手有足够的空间抓取零件。
机器人通过视觉系统实现目标物的检测识别和定位。传统检测识别技术有基于分割的方法、特征分析方法、图像识别决策分类方法、模式学习和形状匹配方法等,这些方法在工业领域得到广泛应用。
机器视觉检测识别技术是用机器视觉代替人眼对工件进行检测、测量、分析、判断和决策控制的智能测控技术。与其他检测控制技术相比,主要包括如下优点:具有比人眼高超的一致性和重复性,智能化程度强;多方面感知外界信息,能够通过多种成像方式获得静态空间、动态工件、结构等信息;检测速度快、准确率高,漏检率和误检率低;具有很好的实时性,可实现快速大批量在线检测;机器视觉与智能控制技术结合,可实现基于视觉的路径策划及高速运动控制、视觉伺服、精确定位识别和作用力的优化控制,极大地提高控制精度。因此,机器视觉技术已经广泛应用于精密制造生产线、工业产品质量在线自动化检测、装配自动化生产线等多个领域中,在提高智能制造装备的精密制造水平,提高汽车、电子、医药、食品、工业产品质量检测效率等方面发挥巨大作用。
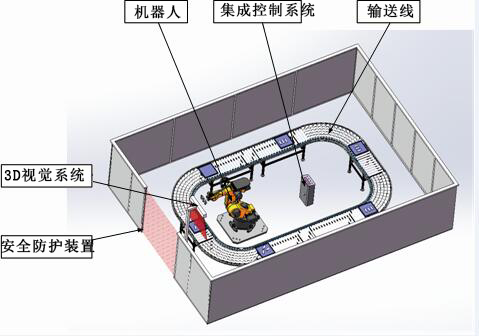
分拣单元组成图
随着工业自动化的发展,机器人分拣技术被广泛地应用在制造、装配自动化生产线上。传统的机器人分拣技术大多采用示教的方式,分拣机器人对工件的初始和终止姿态及摆放位置要求比较严格,这种分拣方式不仅分拣速度慢、效率低,只要工件的摆放位置发生变化就会导致机器人无法抓取零件,从而严重影响生产过程的工作效率。基于视觉系统的分拣机器人具有效率高、错误率低的优点,并且能够保证分拣工作的质量。因此,人们把研究方向转变到机器视觉领域,将视觉技术与机器人相结合,使工业机器人具备类似人眼的检测识别功能,使得机器人在分拣过程中更加柔性化、高精化、智能化,对于降低生产成本、确保产品质量、提高生产效率等方面具有重要意义。
目前,机器人视觉系统已经普遍地应用在工件无损检测、零件参数测量、食品包装、医药生产、物流分拣以及PCB制图等领域,基于视觉系统引导的机器人技术也将成为未来发展的主要趋势。本文针对从生产线上托盘中的堆积零件中抓取工件并规则摆放,提出了一种分拣机器人的定位识别方法,以库卡公司的KR 30型6轴工业机器人、环形输送线等为基础,搭建了基于PLB-500的3D视觉系统工业机器人分拣单元,制定了详细的视觉分拣方案。
分拣单元的组成
随着工业零件的复杂化,在工业生产和装配的过程中,经常出现零件随机散乱放置的情况,因此本文设计一种分拣单元,模拟了乱序零件的工作情况,并通过机器人视觉系统进行引导分拣零件。整个分拣单元由KUKA KR 30机器人及其控制器、输送线、3D视觉定位系统以及安全防护装置等组成,分拣单元的结构组成如图所示。
输送线
本单元采用环形辊筒输送线,起到辅助工业机器人分拣和方便循环展示的作用。输送线中分布3个阻挡气缸和4个光电开关,其具体分布位置如图所示。阻挡气缸用于在特定位置挡停移动的托盘,以控制分拣工作的时序,阻挡气缸3同时还起到撞乱托盘中的有序零件的作用。光电开关用于检测是否有托盘通过,若有,则将信号传输给控制系统,以控制输送线的转速。输送线中放置了5个托盘,其中4个托盘放置零件,一个空托盘用于放置机器人从乱序托盘中抓取的零件,并在空托盘中按规则顺序摆放。
3D视觉定位系统
传统的分拣机器人定位系统存在着定位误差大、识别速度慢和准确率低的缺点,对于复杂的工件,在生产和组装时需要对工件进行人工识别搬运和定位。目前广泛应用于分拣的机器人只能按照预定规划的路径进行运动,对于散乱堆积的零件无法处理。因此,需要一套3D视觉系统,可以识别复杂散乱的工件,并能够给出工件的位置与姿态,引导机器人抓取。
本单元采用Sick的PLB-500机器人导向系统,通过3D视觉系统捕获零件的相关信息并引导机器人进行定位抓取,PLB-500有很大的扫描范围,不受外界光和对比度的影响,可以精确的读取工件的三维信息并传输给机器人进行动作引导。
PLB 3D视觉系统包含:3D相机、易于集成和通讯的零件定位软件。其中3D相机能够适应不同的工作环境,提供准确且可靠的三维图像并且不受人工环境光的影响,并且能够提供较好的图像质量。该系统具备可靠性和易用性的特点,它能毫无问题地集成到现有环境中,提供高精度的测量结果并且非常有助于零件操作的灵活性。
PLB 3D视觉系统,是用于高精度定位杂乱放置于箱子中的零件的一套视觉系统。它使得工作站更换新的零件变得更简单,并能够通过以CAD为基础的3D模型匹配零件的软件来缩短更换零件的时间。
视觉定位系统在分拣作业中的应用
抓取系统组成
完整抓取的系统包含:PLB系统(包含视觉传感器、软件)、机器人控制器、机器人、分拣末端执行器、托盘及工件。PLB系统的视觉传感器主要用于零件三维数据的采集;软件的主要功能为定位容器中的零件,检查给出零件的夹紧位置,并与机器人进行通讯。机器人控制器通过编程控制机器人的抓取路线。
标定
通过标定,可以将相机坐标系转换为机器人坐标系,系统经过转换后直接输出机器人的坐标与姿态,无需机器人做转换。标定时需要将标定物(圆锥)安装在机器人手臂上,将机器人TCP点标定至圆锥尖上。
标定的方法步骤:将圆锥标定物移至相机视野中;相机扫描圆锥;在软件中(AlignmentGUI)输入圆锥尖在机器人坐标系中的坐标;在VOI中不同高度不同位置重复以上步骤;软件自动计算坐标系转换关系,输出转换关系文件并加载至PLB Studio中。
PLB系统使用
PLB系统在定位时,会首先搜寻匹配容器(Bin)的位置,即VOI(Volume of interest)。在经过标定后,PLB studio会在机器人基坐标系中显示容器的位置。
PLB系统的编程软件提供可视化编程,只需将工件的3D模型的CAD文件(.igs、.step)导入至PLB studio,调整其位置即可,抓取位置能够可视化调节(允许一个工件使用多个抓取姿态与抓取位置)。
分拣的工作流程
首先将零件的三维模型导入PLB studio。人为将机器人面前的托盘中的工件随机散乱放置,PLB-500的3D相机扫描识别托盘中的工件,与机器人建立通讯,机器人一次抓取一个工件,将工件规则的摆放在空托盘中;摆放完成后,挡停机构1和挡停机构2收回,输送机运行;光电开关4检测到托盘后,加速段辊筒增加转速,光电开关3检测到托盘后,加速段阻挡气缸3升起,托盘撞到挡停机构导致工件乱序;然后阻挡气缸3收回,托盘被输送到挡停机构1位置,此时空托盘恰好输送到挡停机构2位置,挡停机构1和挡停机构2升起,PLB-500识别托盘中的工件,然后机器人依次抓取乱序工件放置在空托盘中,依次进行循环。
结论
基于KUKA KR30机器人的分拣场景,集成3D视觉定位、智能安全等系统,实现了散乱堆积零件的快速分拣,同时也为机器人产品功能安全认证和系统功能安全评估及智能传感器验证服务提供实操场景。
评论
加载更多