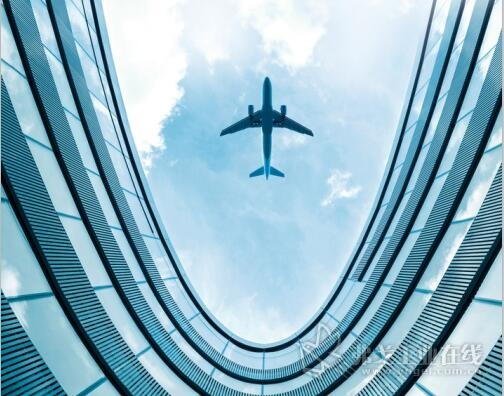
世界知名飞机制造企业信任Electroimpact公司研发的装有Galaxie传动装置的高性能机器
航空航天工业对复合材料结构件生产的自动化步骤的复杂性、精密度和可重复性有最高要求。位于美国西雅图附近的Electroimpact公司是一家世界知名的为航空航天工业提供机器和自动化解决方案的公司。该公司为满足航空航天工业客户对复合材料结构件生产的自动化步骤的高要求,选择了Wittenstein SE(威滕斯坦集团)的具有扭转刚性且无游隙的Galaxie传动装置。迄今为止,该结构尺寸的传动装置的性能数据还是超乎人们想象的,且该设备组合也是世界上独一无二的。在此,也证实了Galaxie传动装置是Electroimpact公司制造的最新一代高性能机器的推手。
Galaxie传动装置基于传动运动学技术的新专利。该创新的核心是:带有全新研发的多边形内圈的滚动轴承和一个分段的轴承外圈。由于采用了两个最新研发的零件,使得该外径同轴空心轴传动装置达到了新的技术水平,与可比较传动装置相比,这种Galaxie传动装置的最大扭矩最多可加大170%、过载安全性最大可提高3~6倍,空心轴的直径最大可加大70%。这仅仅是新类型传动装置的几个性能特性。正是这些性能特征为Galaxie传动装置的设计师们开辟出全新的前景,如新类型Galaxie传动装置在美国一家复合材料结构件的专门生产厂家Electroimpact公司的应用便是如此。
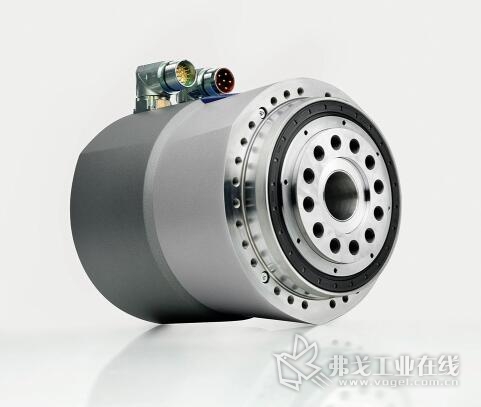
图1 在Galaxie传动装置内将一个带有动态调整的单齿的全新传动装置和一个新研发的高性能电机结合在一起,以确保空心轴传动单元的结构极其紧凑
飞机制造业的自动化设备
Electroimpact公司项目涵盖有民航飞机机翼的全自动化安装系统、用于飞机机翼和舱体安装带有工具的铆接机、高度发展的纤维放置机(Fiber Placement Maschinen、航天飞机的安装机器人系统以及控制系统)。空客公司、波音公司、庞巴迪公司(加拿大国际交通运输设备制造商)、安博威公司、川崎重工业株式会社、三菱重工、富士重工业株式会社、全球最大民用飞机结构件与系统公司(Spirit Aerosystems)、Vought公司、诺斯洛普·格鲁门公司、以色列飞机制造工业公司、中国西安飞机制造公司、美国国家航空航天局和美国通用电气公司等均是Electroimpact公司的客户。
Electroimpact公司将成为航空航天工业的世界领先的自动化设备供应商视为自己的使命。除了其他解决方案外,该聚焦在工程技术方面的企业研发出了AFP(自动光纤放置)技术(Automated Fiber Placement),可以按照客户所要求结构件最终装配的允许公差,以最大为2000 in/min的进给速度在复杂的结构件斜面上完成接合处和断面材料涂层作业。结构件认证的层压材料进给速度为4000 in/min。所有层压过程全部是双向实施的;操作人员可在对接合处精密度无任何影响的情况下操控层压材料进给速度。
Electroimpact公司坐落在距离波音公司仅有几公里之外的地方,波音公司这家著名的飞机制造生产厂家信任Electroimpact公司的高性能机器。为了研发和批量生产将来建造波音777X型飞机的复合材料轻结构件(Composite Leichtbauteilen),Electroimpact公司以最新的技术标准设计出了4台被称作是AFP(自动光纤放置)的机器:此前,还未生产过最大长度为33.5 m的前后机翼翼梁。生产前后机翼翼梁需要3个工作步骤。将所采用的一个机器人集成到一个移动的宽为6 m的门式结构里,机器人的顶部重约0.5 t,以最大的精度将数百层环氧树脂浸渍的碳纤维条和带材料放置在基础结构上。在安放一条碳纤维带材料之后,机器人顶部转动180°,进行重新定位,并在相反的方向上放置下一条碳纤维带。为此,飞机机翼翼梁AFP(自动光纤放置)机器要能够实现机器人顶部可转动±90°,以便能够在一个工序中就能够完成U形结构的飞机机翼翼梁的加工制造。在飞机机翼翼梁的加工制造中,Electroimpact公司将一个重量约为1.5 t的机器人顶部集成在一个12.8 m宽的移动门式结构里。
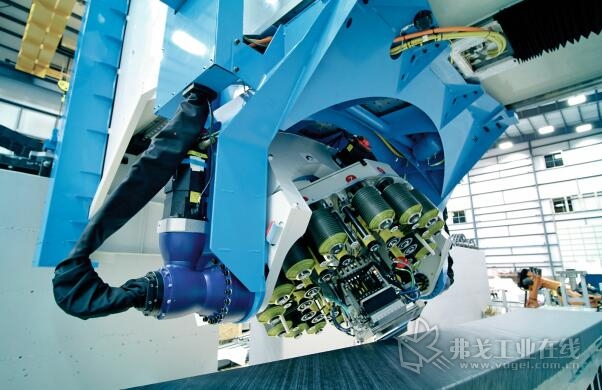
图2 在完成一条碳纤维材料带的放置后,机器人顶部转动180 °,重新定位并在相反方向放置下一条碳纤维材料带
这种新制造工艺的优势是多方面的。由于材料放置明显加快,故加工流程周期明显变短,机器的生产能力便大大提高。现在,可旋转的机器人顶部能够对像飞机机翼翼梁的类似作业条件,严苛的外形尺寸复杂的工件实施更加高效且省时的加工作业。可旋转的机器人顶部可对类似单片式的外形尺寸复杂的飞机机翼翼梁实施加工作业,由此便提供了通过采用及其轻的结构形式对正式的飞机结构实现自由创新的最大可能性。值得注意的是,由于从两部机器的16和20个卷轴里同时并行抽出仅几厘米宽的碳纤维材料带,并将其以迄今为止前所未有的精密度毫无漏洞的并排放置。由于碳纤维材料带高精准度的并排放置,省去了再修整的作业。所加工制造的飞机机翼以及翼梁便具有重量更加轻以及结构更加纤细和空气动力学性能更加优化的优点。
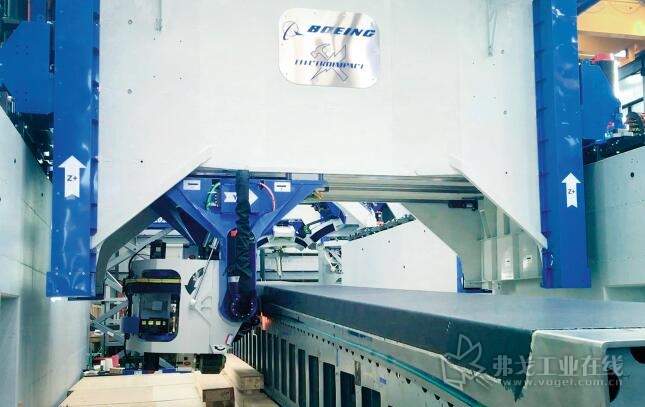
图4 一个重量约为0.5 t的机器人顶部集成在一个宽6 m的移动门式结构里, 高精密度的将好几百层环氧树脂浸渍的碳纤维材料条和带放置在当时作业的基本结构上
飞机部件制造流程高生产效率的前提是,移动式门式结构具有高运动精密性和重复准确性,且可旋转的机器人顶部具有灵活性。Electroimpact公司的工程师们在AFP(自动光纤放置)机器里使用了Wittenstein(威滕斯坦集团)的Galaxie传动装置,从而采取了一个新的解决方案,该解决方案可完全满足高技术要求,并由此提供潜在的可能性。Galaxie传动装置所具有的决定性优点是高旋转性能和完全无游隙,在碳纤维放置流程中当材料放置方向发生变化时,这些性能够确保所放置的碳纤维条和带材料的准确定位。枢轴里的附件确保了结构的紧凑性,并确保运动控制具有更大灵活性。
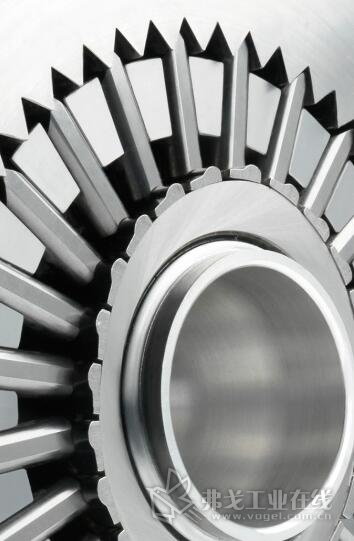
图3 Galaxie传动装置的运动技术特点是动态调整的单齿围绕着一个多边形编组
Galaxie传动装置使生产率提高
Galaxie传动装置通过特殊的结构原理实现了两个精密性能。这些分段的单齿由滚针轴承安置在一个六边形驱动器上,且分段单齿与内齿圈的内齿相啮合。这样的布置和专门的齿面几何尺寸,与通常的传动运动学装置相比便形成了一个最多大6.5倍的齿面,便实现了弯曲长度的最小化以及齿面啮合的宽负荷分布的最佳化。而且,坚实的分段轴承外圈与一个坚实的带齿轴承托架相配合,使得该传动装置与市场上可对比的最佳传动装置相比,扭转刚性可达到之前的150%。Galaxie传动装置的特有结构是Wittenstein(威滕斯坦集团)的专家们研发的单推力齿运动技术装置,该装置通过靶向的内啮齿制成无游隙传动装置。与此同时,在接触中形成的流体运动润滑膜又使得定位传动装置在范围内实现最高工作效率。
由于该驱动装置在整个使用寿命中实现了零游隙,这样,首先确保了门式结构的运动方向的反向回程以及机器人头部运动的最大精准度。从AFP(自动光纤放置)机器的角度来看,Galaxie传动装置所具备的这些性能,首次实现了单批次生产作业仅生产一个高度复杂的飞机复合材料结构件,且生产达到了前所未有的高生产率。
评论
加载更多