工业4.0这一主题早已与注塑机制造商息息相关。工艺监测和控制的网络化与数字化可提升注塑工艺过程的透明度,并可以从经济效能上优化生产过程,而实现这种注塑工艺网络化的基础则是智能的工具传感器。例如瑞士Kistler公司提供的传感器,该模具中的传感器能对工艺过程进行监测,并使该过程更加透明,工作效率也将因此得到提高。

在虚拟环境中整合传感器获取的数据,不仅可以监测和优化各个注塑成型周期,还能监测和优化整个工艺过程。模腔压力监测需要自动或者手动设置好待测部件,然后观察传感器输出的曲线是否按照预定方式通过待测部件,再根据结果显示“正常”或“异常”便可将这些部件按照好坏进行分类。此外用户还可以基于模型对明确的质量特性进行预测,根据在线质量预测为基础,能够预先对每个成品部件做出可靠的评估。
传感器的安装位置
通过在注塑模具中使用传感器不仅可以测量出模腔压力,还能检测出温度控制器在进料和回流时的温度和流量。来自Burkert流体控制系统公司的Martin Schramm指出:“温控过程越理想,产品质量越高。”就工业4.0中注塑成型工具的使用而言,传感器发挥了重要作用。由传感器组成的控制系统能够通过整合I/O链路使调节器和阀门网络优化。来自德国RJG公司的Ulrich Bretthauer强调了传感器对最终产品质量的重要性,他指出:“一旦塑料离开了注塑机的喷嘴,加工人员就会变得束手无策,受制于腔内的物理定律以及待处理材料的粘度变化。如果可以成功地使用模腔压力技术,将能够稳定注塑工艺过程,并最终降低成本,提升公司的竞争力。然而想要实现这些,仅仅依靠在某处安装传感器,观看漂亮的曲线是远远不够的。
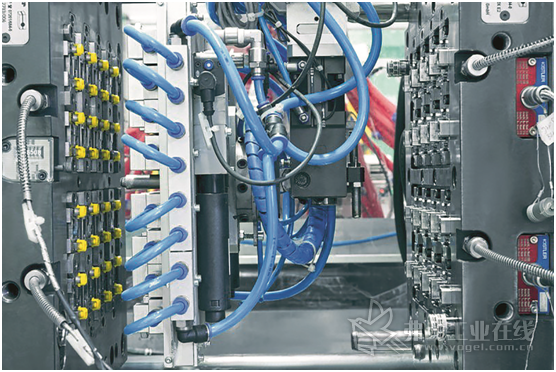
图1 数字化时代的数据传输就离不开广泛应用的传感器技术,例如,当注塑模具配备有传感器时,就可以存储和跟踪直至各个模腔内注塑成型的模态,并在出现问题时快速找到应对方案
传感器在模腔内所安装的位置决定该技术所起的作用,到底是带来收益还是仅导致成本升高,这点同样适用于注塑工艺装置和压力曲线评估。Bretthauer特别指出:“对于每个新项目,首先必须明确传感器应该完成哪些任务,因为这将决定安装传感器的位置。”模腔压力传感器通常用于控制工艺过程,即保压切换、打开和关闭喷嘴以及工艺过程监控。虽然针对传感器安装位置能给出一些简单的基本建议,例如大多数时候可以靠近注塑口,但是要想确定安装传感器的最佳位置,通常还需要对流量和压力情况进行模拟。

图2 由Kistler提供的在线工具Comoneo可用于塑料加工过程的高端过程监控,这种参数监控符合 “注塑4.0”的要求
工艺过程透明
模具中传感器可以对模具中的压力和温度进行组合测量。来自Arburg注塑机制造公司的应用技术部负责人Thomas Walther博士指出:“使用传感器归根结底就是为了使模腔内的状态可视化。”这意味着加工人员可以通过传感器获知“黑匣子”内当前的运行状况,机器操作人员则可通过模具传感器直接获取信息。
这样一来用户便能更加详细地对工艺过程进行设置,并使其具有更好的可重复性。Walther强调:“加工人员能够通过模具中的传感器更好、更深入地了解封闭的系统,还可以更好地理解工艺过程和优化过程控制,工艺过程的可重复性最终能够提高生产部件的质量。
Arburg注塑机的控制系统可以通过调节参考曲线对与压力和温度相关的信号进行处理,这将进一步细化和改进干预措施,控制系统会记录由传感器提供的相关过程参数,当其与MES系统结合在一起使用时,将有助于生产工艺过程朝着工业4.0所要求的自动化和网络化方向发展。

图3 图中是Sensopart工业传感器公司生产的一部用于注塑模具的工业视觉传感器,该传感技术可以检测出由于过度注射或注射不足导致的缺陷部件以及安装错误的部件
与注塑部件生产和组装有关的工艺过程为最新一代能够处理图像视觉的传感器提供了广泛的应用空间。Sensopart传感器公司的Klaus Berdel指出:“通常注塑成型过程中最常见的问题是短射引致的模具不完全填充以及过度注射导致的毛刺和飞边。”利用预置好的工具对工件的表面和轮廓进行检测很容易发现部件的几何形状有这样或那样的偏差,此外视觉传感器还能够及时检测插入错误,例如在注塑问题的模制插头中发现未校准的金属销。
Toses Tooling Security Services公司的Burkhard Walder认为,在注塑模具中使用传感器可以降低维护次数、延长模具使用寿命、减少不合格产品、及早发现工具损坏和监控工艺参数,从而使整体设备效率得以提高。他总结说:“所以说传感器对提高生产效率做出了重大贡献。”例如,该公司的传感器系统可以根据模具的噪声发射情况来优化维护周期。在使用该系统时,只需要根据实际需求对模具进行维护,而不是根据生产的部件数量,因为传感器能够对模具中的噪声进行检测,并以此确定出急需维护的模具。

图4 Kistlers公司的ComodataCenter适用于注塑成型过程的数据管理和分析,此外该工具还连接了Comoneo和Como Injection系统
TE Connectivity公司的Felix Eggert强调说:“注塑模具中使用传感器可以提高模具的生产质量和生产效率,尤其是温度必须经过精确测量,才能对生产部件质量进行监控,无论是温度过高或过低,还是温度的小幅变化都会对质量产生决定性影响,例如在稍高的温度下,部件就会有可能燃烧。此外,传感器还能使质量欠佳的部件自动分拣出来,在使用敏感的温度传感器时,不合格的产品数量会下降,生产效率也可以得到提高。”
德国Gefran公司的Kai Wiegand解释说:“模具压力也可以通过对注塑机螺杆的应变测量来确定,目前这种压力传感器还没有集成到注塑模具中。压力传感器能够记录螺杆上的受力,并使信号经过放大器抵达控制系统进行评估。”
注塑成型过程复杂多变
对传感器提供的信号评估和处理是生产高质量注塑件的先决条件,当然高精度注塑模具也是必不可少的,例如想要使生产部件公差小于30 μm,就必须使用误差低于10 μm的注塑模具。此外,还需要用于模具补偿的测量传感器,例如Carl Zeiss工业测量仪器公司就为此发开了一种用于表面反馈的创新软件。
Priamus系统技术公司把注意力集中在模腔内的传感器上,该公司德国部负责人Erwin Konig认为注塑工艺是一个非常复杂的制造过程,需要不断调节,所有的调节都会对注塑部件的质量产生或多或少的影响。此外该工艺过程还会受到多变的外部影响,这些外部变化对部件质量有决定性的影响。
为了使实际生产过程以及对过程中的波动一目了然, 模腔压力传感器和模腔温度传感器必须安装在注塑模具的模腔内,以提供高清信息。Konig断言:“正如测量的普遍规则,往往离工作地点越近,越容易获得最好的高清信息,所以说由注塑机或成像系统提供的信号往往不具有这么高的说服力。”
评论
加载更多