Anger的加工中心如今在知名供应商处为戴姆勒、大众和Stellantis生产汽车零部件。在生产中,工件由Kosmek零点夹持系统精确定位和固定,然后在5个轴上对电池托盘、侧裙、A柱、纵横梁或铝型材进行铣削、钻孔和去毛刺。
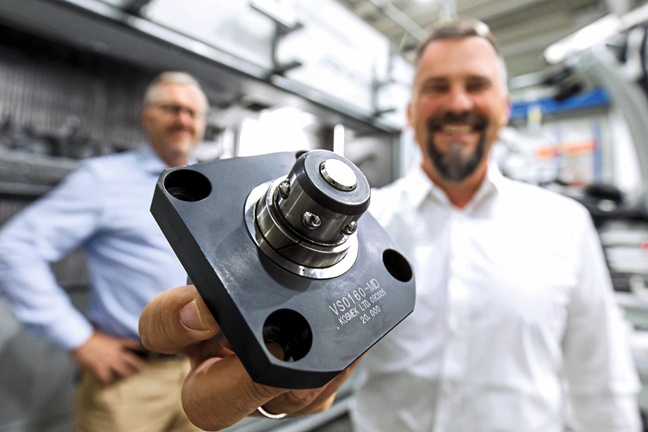
Kosmek的零点夹持系统
“为了能够充分应用机器功能,必须将安装时间压缩至最短。”Anger Machining的首席问题官Dietmar Bahn解释道。由于需要极高的重复精确度,所以零点夹持系统起到了核心作用——它们将工件与机床工作台连接起来。
在最新一代的SP系列产品中,1台机器上可以有1个、2个或4个主轴同时加工多个同名结构部件、电池托盘和用于电动汽车的挤压型材。这些薄壁工件有些长度超过2 m,极易受到振动,需要非常特殊的夹持系统。
Andreas Roithmayr解释说:“需要一种高度动态的大型机器,它可以同时加工多个零件,快速装载大型部件,精确夹紧并精确加工,而且还能很容易地进行改装。”
Anger Machining的技术销售和产品管理部门经理继续说道:“这是一种难以实现的平衡状态。”
自2018年以来,Anger的第一台SP系列产品一直在为戴姆勒加工A柱,如今系列产品和任务的复杂性大幅提升,人们长期以来一直试图在批量生产中挤出最后的0.1 m,Roithmayr以为一家德国集团灵活生产地电池托盘为例。
“凭借其优势,Kosmek零点夹持系统在安装过程中发挥着重要作用,这里损失的时间会降低系统的有效性和产出,这些损失的时间在加工过程中再也无法弥补。”Roithmayr强调说。除了零点夹持桥,Anger还使用零点夹持套,它们使员工们能够快速更换工件,无需将整个夹持桥从机器中抬起,借助室内起重机、夹具机械手或装配车辆,即使转换两个大型电池托盘也只需要10 min,无需复杂的测量回路即可批量生产新组件。Kosmek的液压零点夹持系统的重复精确度可达3 μm,因此加工中心不再需要对齐检查。
“由于不再需要这种复杂且耗时的调整和校准过程,可以节省数小时。”Anger Machining的销售主管Dietmar Bahn解释道。
评论
加载更多