Hirata 是一家为汽车行业制造商提供生产设备和工程服务的知名供应商。借助最新的制造技术来改进系统,Hirata 利用其大型组装调试空间和洁净室模拟大型生产系统,并创建灵活的流程,帮助最终用户应对不同地区不断变化的市场需求。Hirata 的最终用户已经习惯于能够实现高质量且高效系统的卓越工程能力。
为了满足这些期望,Hirata 使用了独一无二的设计方法,即装配单元系统 (ACS)。ACS 是一个流水线系统,能够以比传统系统更快的速度、更低的成本和更好的性能创建出可靠的生产系统。ACS具有高度标准化的模块,通过分析各单元、机器和部件的运行与功能,可以加速投产。
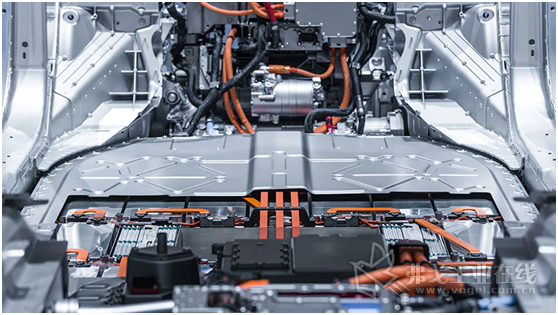
Hirata为客户开发的定制电动汽车电池生产机器必须比传统机器小,比相同生产规模所需的常规机器占地面积小30%。为了实现按时交付并减少占地面积,Hirata希望为整个解决方案使用单个供应商——即一个能够提供本地支持以加快调试速度的合作伙伴。
Hirata还使用了来自罗克韦尔自动化系统集成商的其他资源。由于这是行业第一台期限极其紧迫的机器,团队需要实时地规划和应对挑战,并在海外最终用户所在地调试整个系统。
Hirata之所以选择罗克韦尔自动化公司,部分原因是该公司具备提供全球支持的能力。Hirata的内部生产工程能力和处理新类别的能力,即“Monodukuri”制造能力,创造了业界第一条电动汽车电池的大规模生产线。
可通过缩短设备安装和调试时间加速投产。通过标准化零件简化了装配线,从而减少了占地空间,便于维护。缩短了装配线,减少了在制品库存。易于适应产品变化或未来装配线变化。支持通过改变设备数量或布局来改变生产产量。在制造过程的每个操作中使用的设备和零件都是标准化的,并集成到“标准化模块”中。每个模块都配备了一系列适用于不同制造工艺的功能。标准化可提高产品质量,减少设备故障。
Hirata最初使用其ACS的标准单元开始机器设计;但是,鉴于减少机器占地面积的需求,Hirata需要使用一个ACS进行多个操作。为了实现这一点,Hirata分析了每台设备的运行情况,并采取了一种新的方法,将多达四个操作合并到一个工作站中。为了实现这一理念,Hirata将多个部署到一个ACS中。台架由Kinetix® 5700伺服驱动器控制,最多支持23个轴。每个轴需要同步高速运行并可在三个方向上移动,无需人工干预。
在罗克韦尔自动化公司的支持下,Hirata设计出了优化的轴结构和编程,并使用新的ACS理念成功创造出了更小占地面积、大规模、高速、高精度和精密的生产机器。机器通过以太网连接到最终用户的制造执行系统(MES),因此可利用机器数据支持实时远程诊断和维护。Hirata可以从世界任何地方访问机器数据,从而消除差旅成本。
对Hirata来说,最重要的指标通常包括循环周期、运营率和收益率。这一次,Hirata还将占地面积减少计算在内。罗克韦尔自动化产品的标准化提高了总效率。内置的用户自定义指令(AOI)功能可将编程时间缩短30%左右。此外,标准化产品以及与罗克韦尔自动化公司的合作将机器占地面积减少了30%。在罗克韦尔自动化日本公司的支持下,团队可以快速提供现场支持,投产时间缩短10%。Hirata实现了按时按用户要求批量生产电动汽车电池的目标。Hirata在与罗克韦尔自动化公司的合作下,又向前迈进了一步,能够通过其大规模生产线满足不断增长的电动汽车电池需求。
评论
加载更多