近日,西门子数控(南京)有限公司(SNC)新工厂正式投运。作为西门子全球首座原生数字化工厂,SNC新工厂全面展示了西门子先进数字化企业理念与技术的切实价值。在实地建设之前,西门子就已全方位应用自身数字化技术,预先在虚拟世界打造工厂的数字孪生,实现从需求分析、规划设计、动工实施到生产运营全过程的数字化覆盖。
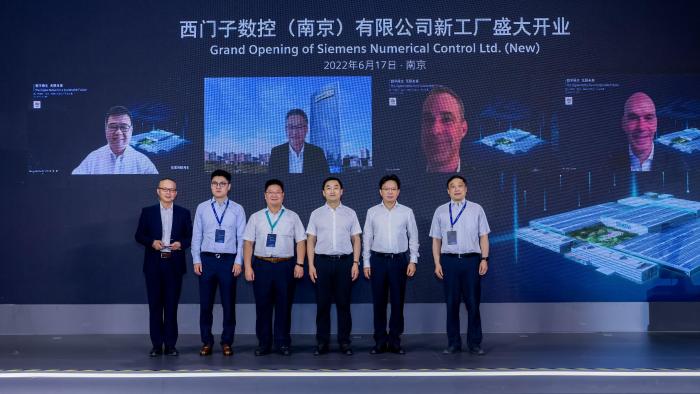
图1 西门子全球首座原生数字化工厂在南京正式投运
SNC成立于1996年,主要产品线覆盖数控系统、通用变频器、伺服电机和齿轮马达等产品,广泛应用于汽车、航空、电子、制药、物流和新能源等高端制造行业,并有大量产品出口海外市场。作为西门子运动控制领域德国以外最大的研发和制造中心,SNC近年来面临日益增长的市场需求,急需扩大产能,提高生产效率和灵活性。而基于西门子自身数字化技术打造的原生数字化工厂在智能灵活的产品和生产设计、集约高效的生产运营以及基于数据驱动的优化服务等方面都拥有巨大优势。
原生数字化的力量
“从设计、规划、建造到生产运营的全生命周期,从0开始,开创性的完全使用西门子自身的数字理念和技术,让工厂从无到有,由虚到实,这就是原生数字化的概念。”西门子全球执行副总裁,西门子中国董事长、总裁兼首席执行官肖松博士在媒体采访中表示,“在工厂破土动工之前,我们已经在虚拟世界里用西门子自己的软件,完成了从工厂需求、分析到建成、运营全过程模拟仿真和验证,同时在实际建设的时候,我们通过大数据的分析,进一步优化生产流程,为实际生产提供实时可靠的数据支撑,实现数字制造和管理,达到持续优化的闭环。”
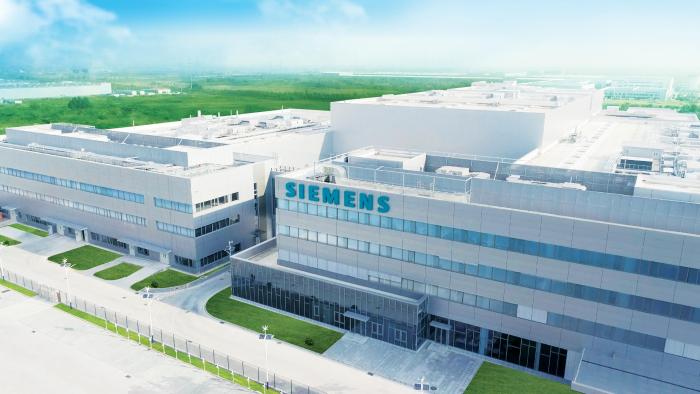
图2 西门子数控(南京)有限公司新工厂
从产品的研发环节、到制造环节再到用户端应用环节构成了一个产品的生命周期。当产品全生命周期中产生的大量数据能够互联互通,在此基础上去探索数据和数据之间的逻辑关系,用这种算法再来支撑产品研发、生产制造,为用户提供可决策的信息,这样的闭环便是智能制造的精髓所在。西门子(中国)有限公司执行副总裁、西门子大中华区数字化工业集团总经理王海滨谈到:“从底层逻辑来讲,西门子成都工厂和SNC新工厂本质上都体现了智能制造‘工业4.0’的场景。而这两个工厂的区别在于,几年前成都工厂建成,是有德国安贝格工厂做参考和样板,而SNC新工厂更多的是依靠本地同事的智慧和经验,大量使用了西门子数字化企业的产品组合和技术手段,从而实现了新工厂的建设。”
据悉,新工厂投产之后,产能将提高近2倍,生产效率提升20%,柔性生产能力提升30%,产品上市时间缩短近20%,空间利用率提升40%,物料流转效率提升50%。新工厂可同时生产电子和电机制造两大类从原材料、生产设备到工艺流程均截然不同的产品。
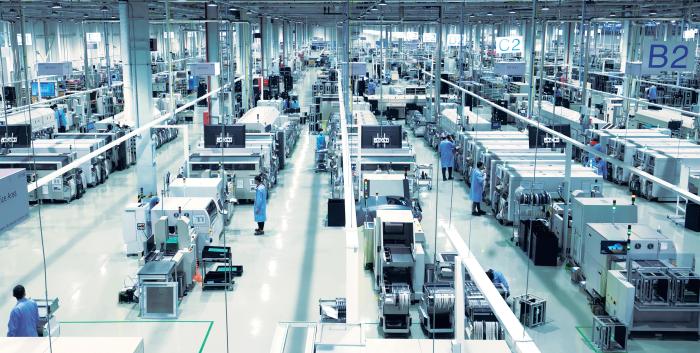
图3 西门子数控(南京)有限公司新工厂
数字产业化是“终极目标”
谈及西门子工厂如何赋能用户加速数字化转型,王海滨表示,已经退休的原西门子股份公司数字化工业集团运动控制部CEO Wolfgang Heuring博士曾经提出,我们不仅要建成生产自己的电机、数控系统产品的工厂,也要使SNC新工厂成为数字化转型的体验中心、赋能中心。因此西门子在设计工厂时,已经把体验中心、赋能中心、能够与客户进行价值共创的场所以及背后要展示的内涵,纳入新SNC的设计考虑。由此也能够体现出,西门子不仅助力自己的工厂成为原生数字化工厂,也将原生数字化技术贡献于中国各行各业的制造业同仁,真正地践行产业数字化,而下一步,则是让数字化手段走向千家万户,这便是数字产业化。
低碳环保也是西门子在规划SNC新工厂之初就重点考虑的因素。该工厂采用多项国际先进的低碳环保技术:利用屋顶光伏系统为工厂运营提供部分清洁能源;利用地源热泵技术提高冬季供暖和夏季制冷能效;应用高效率水泵和风机、热回收装置、雨水回收系统、风能和光伏LED路灯、智能照明控制系统和太阳能热水系统,最大限度地节能减排。各项节能减排措施将共同助力SNC新工厂成为一座绿色高效的低碳示范工厂,预计每年可节省约506万kW·h的电力,6286 m3的水,减少3325t的碳排放。
2022年是西门子与中国同心同行的第150年,SNC新工厂的启用也充分表明,西门子以本地化的完整价值链和全球资源,助力中国社会和经济的高质量发展。
评论 0
正在获取数据......