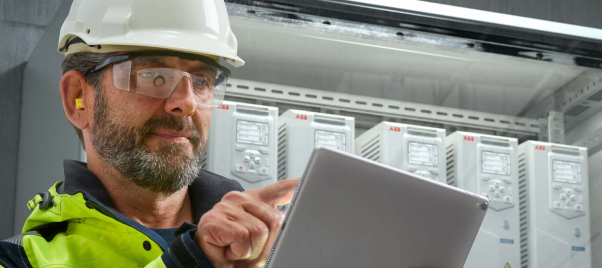
ABB委托Sapio Research进行了一项全球性调研,并于近日发布了题为《可靠性的价值》的调研结果,显示了工业企业的高停机频率与由此导致的高昂成本。本文将探究产生停机成本的根本原因,以及工业企业可以采取哪些措施防止停机。
对于全球工业企业而言,非计划停机一直都是造成生产受挫和现金流不确定性的一个主要原因。调研结果显示,在全球范围内,典型工业企业每小时的非计划停机成本近90.9万元,在中国这一数字约为63.6万元*,这一差异可能是由于劳动力的相对成本造成的。
谈到该调研结果,ABB运动控制事业部中国区负责人戚鲁平表示:“停机并无标准时长,如果按照停机时间为一个工作日即8小时计算,企业每日损失将超过数百万元。鉴于此,工业企业应该致力于从高风险的被动维护方式过渡到可靠运维保障策略。这将帮助企业在提高可靠性和商业声誉的同时,加强竞争力,降低成本,助力企业专注于提高其核心竞争力。”
ABB委托Sapio Research于2023年7月开展了这次调研,共收集了全球3215位工厂维护决策者的反馈,涉及能源电力、塑料和橡胶、石油和天然气、风能、化工、铁路、公用事业、海洋、食品饮料、水及污水处理以及金属11个行业。调研发现不同行业的停机成本存在差异,具体可能受到监管机构对不达标的处罚、回头客的流失、声誉和士气受损的影响。
停机成本可能会迅速增加。直接成本来自于维修和备件、生产损失、原材料浪费、操作员空闲和可能的清理费用。44%的中国受访者表示,其所在工厂每月至少经历一次非计划停机,而在全球范围内这一数字为69%。这会引发业务风险和生产中断。
这也就不难理解, 60%的全球受访者表示,计划在未来三年内增加在可靠性和维护方面的支出,以期达到如下几大目标:50%的受访者希望减少非计划停机,55%的受访者希望提高能效,51%的受访者希望延长设备寿命,51%的受访者希望提升客户需求响应速度。
不断演变的维护策略
本次调研的一个显著结果是,很多用户没有优化其维护工作。随着维护策略不断变化,很多工业企业开始使用更为先进的服务来保持设备运行。
尽管如此,仍有21%的全球受访企业还在采用故障后再处理的维护策略,即等到设备出现故障后,再去维修。采用这种被动维护策略,必然要承担停机的代价。调研显示,80%采用被动维护策略的生产基地每月至少经历一次停机,远远超过69%的平均水平。
45%的受访企业采取了基于运行时间的维护策略。这一策略可以有效提高可靠性,但往往成本较高,因为在此过程中会更换仍可正常运行的设备。此外,这一策略无法识别和解决计划外的问题,因而无法排除风险。
另外一种行之有效的维护策略是:基于状态维护或预防性维护。调研显示,三分之一的受访企业利用运行数据,可在设备发生故障前很长时间监测到风险和问题,并提醒维护经理采取措施。
提高可靠性的下一步举措
随着技术和新业务的发展,一种新的维护模式——可靠运维保障策略应运而生。与根据固定服务时间或单次服务项目的传统维护策略不同,该维护策略根据实际结果(如正常运行时间或节能情况)收费,其核心理念是:通过复杂设备的维护风险外包提升绩效。
调研结果发现,可靠运维保障策略极具吸引力,87%的受访者对该维护策略感兴趣。该维护策略可提高可靠性,并带来诸多其它益处,亦可在不断变化的市场环境中为工业企业提供切实的帮助,同时该策略也有助于弥补资深技术人员退休等情况造成的复杂设备维护技能缺口。调研结果显示,企业可运用新技术并采取主动式的维护策略,从而提升工厂的整体运维能力。
采用可靠运维保障策略还可帮助企业在不断变化的市场中保持稳定的运维成本。用户通过服务合作,提高正常运行时间并降低成本,确保工厂达到稳定运维的目标,从而更专注于企业自身发展,真正做到安心无忧。
*注释:本调研基于第三方根据问卷提供的信息进行,而非实际的会计记录。
文章来源:ABB
图片来源:ABB
转载平台:企业投稿
责任编辑:朱晓裔
审 核 人:李峥
评论
加载更多