为了灵活地满足不同要求,目前的塑料生产设备都已采用了易于更换的模块化液压驱动、混合驱动和电力驱动机构。但在大功率的塑料生产设备中,液压驱动技术凭借其很高的功率密度和坚固耐用性能有着明显的优势。与电力驱动系统相比较,液压驱动系统的维护保养成本更低且几乎没有磨损。现代的液压驱动技术还确保能够向液压系统用户提供符合他们需求的、高效节能的压力供应。数字化控制的、分布式智能化的液压元器件和子系统为优化塑料生产设备的基本功能,例如在塑料生产设备的注塑、开模与合模以及脱模等功能中打开了新的大门。
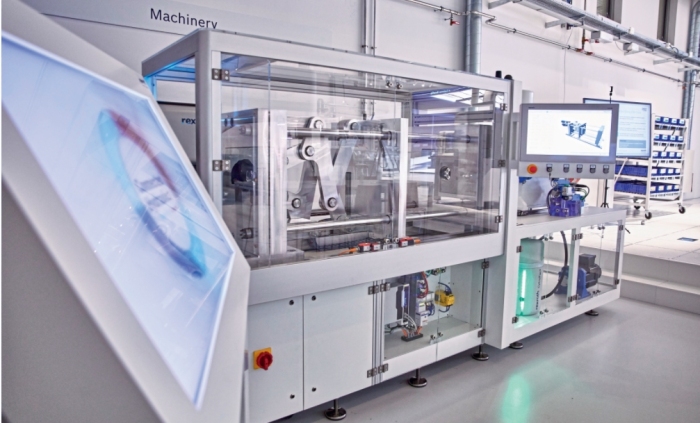
图1 液压技术与数字化控制调节技术的相互融合,以及现场与更高级别系统之间的联网,提高了塑料生产设备的生产效率和生产能力
性能强大的智能化液压泵驱动系统
Bosch Rexroth公司研发生产的Cytrobox型液压动力站是一种性能强大的智能化液压动力系统。它能提供7.5~30 kW的功率,还能为像抽芯机构之类的辅助装置提供额外的工作压力。作为一种即插即用的解决方案,它的安装调试工作量明显减少了很多。嵌入式的IoT物联网服务Cytro Connect解决方案包确保了液压动力站高可用性,避免了液压动力站的意外停机。
该液压动力站的可持续发展性能也因为可通过各种巧妙的“设计杠杆”而灵活地“撬动”,例如Cytrobox的所有组件、部件都配置在狭长外壳的底部,这就使它的占地面积比迄今为止的液压站减少了75%,只需0.5 m2的占地面积。转速可调的变速泵驱动系统Sytronix自身的智能系统就可以通过控制器预设的参数根据液压动力站工况的实际需要主动调节液压泵的转速。这就可以在液压系统循环工作时降低80%的能源消耗。排净了空气和流量优化的液压油箱减少了液压油的需求量——只需150 L即可,不再是原来的600 L了。另外,即使是在满负荷的工作情况下,Cytrobox液压动力站的噪音也小于75 dB。
转速可调的驱动系统
转速可调的液压驱动系统对工业企业液压技术的发展做出了重大贡献。通过调节转速可以节约能源,伺服电机驱动的可变排量泵则通过伺服电机不同的安装角度能够更好地适应不同使用场合的需要。这就使长期或恒压工作时,它们比定量泵有着明显更低的电动机输出扭矩需求和更少的电力能源消耗。
例如,与恒定转速的液压泵系统相比,Bosch Rexroth公司推出的A3V系列柱塞泵在注塑机和其他循环工作的使用情况下可以节约80%的电力能源。由于这种柱塞泵的转速很高,因此A3V2Q045可变排量柱塞泵可以在电动机输出扭矩减少30%的情况下实现相同的流量。这就可以将伺服电机的尺寸做得更小,从而降低液压设备的投资成本和使用成本。根据实际需要调整液压泵的输出流量也是进一步缩小尺寸的可行方案,在许多循环工作的工况中通过调节电动机扭矩还可以再降低30%的电力能源,进一步减小变频器的尺寸,以节约能源和资源。
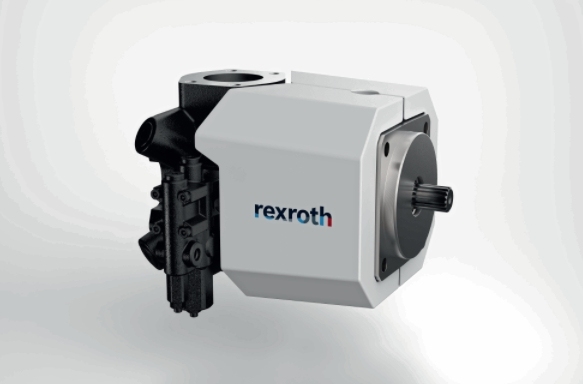
图2 新的A3V2Q045型中压泵的最高转速达到了4000 r/min,工作效率高达93%
将硬件绑定的液压功能转移到软件模块中
随着电液联动技术的发展,液压系统的可控性和集成性也都有了长足的进步。但这种进步仍然像以前一样都是以硬件研发为中心的发展与进步。电子技术和软件技术被“设计为”实现硬件绑定的工具并在实践中得到了落实。如果将硬件绑定的液压功能控制权移交该软件模块,则液压系统制造商的产品将具有更大的使用灵活性。
Bosch Rexroth公司最新推出的H4U(Hydraulics for You)就是追求这种方法的软件平台。H4U软件平台是由不同的软件模块组成的,这些软件模块也统称为液压功能控制模块。根据液压系统的具体要求,这些液压功能控制模块可以相互组合在一起构成一个液压控制系统。它们的功能范围涵盖了从液压系统的压力调节和流量调节,也包括了液压油缸的行程控制和液压力控制直至最高级的控制功能,例如多个液压缸的同步控制等等。
利用H4U平台可以不用像传统的液压系统那样,将专用的控制调节电路与液压控制元器件直接耦合相连。这一平台中的液压元器件控制功能与硬件无关,因此可以方便地集成到机床设备现有的液压控制系统中去。
同样,还可以在一些与工作循环时间关系不紧密的功能中使用。例如边缘云计算解决方案或者云计算解决方案的状态监控。通过这种方法就可以超越机床设备的限制实现更多的增值服务,也就可以在机床设备的整个使用寿命周期内提高它们的经济性和未来适应性。软件平台提供的节约能源和连续性仿真模拟也提高了注塑机械的能源利用效率和可持续发展性能。
工业4.0网络化应用的数字接口
塑料生产设备中所有执行器的联网发展非常迅速。同时,对网络化液压系统的要求也从简单的状态查询发展到复杂的、分布式的同步运动控制。在这种情况下用户只能通过数字接口技术才能在塑料设备生产工作过程中利用软件来更改设备工作参数,灵活地为新生产任务做好准备。
数字化还可以实现设备故障的快速诊断,通过状态监控提高塑料生产设备的可用性。基于云计算的液压控制系统还可以为液压系统的维护保养提供技术支持。模块化的液压系统配置方案使 用户可以根据实际应用的需要和塑料生产过程提出的具体要求有针对性的配置量身定制的液压控制系统。
状态监控
Bosch Rexroth公司借助于Cytro Connect解决方案提供了覆盖面广泛的技术服务内容——从简单的设备状态数据可视化到按照规则的设备状态监控直至预测性的数据分析等。前面的Cytro Connect预测能够基于自主学习的算法语言完成生产设备数据的预测分析。为此,它会在一段时间内记录系统的状态并用人工智能技术形成一个数字化模型,系统会根据这一模型检查设备操作中的偏差,并将显示出这些偏差会导致最终产品出现什么情况。
这就构成了一个基于数字模型的状态分析,不需要操作者目不转睛地紧盯监控仪表并验证是否出现超出极限值的情况。在此基础上,专家们会在早期就给出设备维护保养的建议。这可以将Cytro Connect系统用户设备维护的时间支出减少50%。这些预测性的维护保养措施确保了生产设备最大的可用性,并能有效减少设备配件的库存量。另外,Bosch Rexroth公司还定期提供Cytro Connect系统的性能和使用情况报告,使用户能够在此报告的基础上进一步优化自己的系统应用。
通过将液压功能从硬件转移到软件模块,智能化、网络化的液压系统施工阶段的工作也得到了大大的简化。设计师可以利用相同的液压元器件设计出各种不同的液压系统。这也大大降低了液压系统设备调试的工作量。工作相互协调的液压元器件和软件模块提高了液压系统整个寿命周期内的过程可靠性和重复工作精度。
此外,现代化的液压系统也为减少能源消耗提供了更多的可能性,从而也降低了液压系统用户的使用运营成本,提高了他们的经济效益。通过联网,用户也拥有了新的状态监控可能性。最终用户可以通过诸如Cytro Connect等基于云计算的系统平台使用预测性维护保养方案,从而明显提高机床设备的可用性。
评论 0
没有更多评论了