九江石化以“原创、高端、引领”为方向,以“提高发展质量、提升经济效益、支撑安全环保、固化卓越基因”为目标,将新一代信息技术与石化生产最本质环节紧密结合,从理念到实践、从实践到示范、从示范到标杆,探索出了一条适合石化流程型行业面向数字化、网络化、智能化制造的路径,业已形成经营管理科学化、生产运行协同化、安全环保可视化、设备管理数字化、基础设施敏捷化,智能工厂全域赋能核心业务绩效变革式提升,助推企业高质量发展取得可喜成效。
一、实施路径
(一)搭建智能工厂总体框架。在石化企业典型信息化三层平台架构之上,构建了集中集成、数字炼厂和应急指挥等公共服务平台,实现了“装置数字化、网络高速化、数据标准化、应用集成化、感知实时化”,形成了石化流程型企业面向数字化、网络化、智能化制造的基本框架。
(二)重塑生产运营指挥中枢。生产管控中心实现了“经营优化、生产指挥、工艺操作、运行管理、专业支持、应急保障”六位一体的功能定位,生产运行由单装置操作、管控分离向系统化操作、管控一体转变,有效地支撑生产运行管理变革式提升。
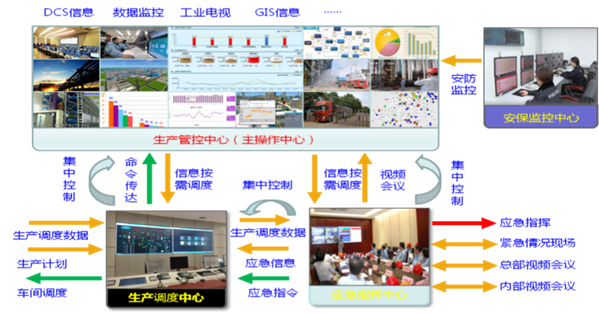
图1 九江石化智能工厂生产管控中心
(三)提升流程管控智能优化。以ODS为支撑,集成MES、ERP、LIMS等重要数据,建立基于核磁技术的原料油快评系统,开发主装置机理国产模型,推广APC应用,试点RTO,实现炼油全流程优化一体化联动优化功效,生产运营由传统经验模式转变为协同优化模式,助推企业经济效益稳步提升。
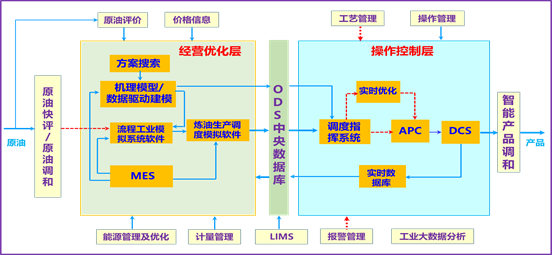
图2 九江石化炼油全流程一体化智能协同优化示意图
(四)构建数字炼厂创新应用。建成与物理空间完全一致的数字化炼厂,实现工艺、设备、HSE管理等六大类深化应用虚拟场景可视化呈现,并通过模型场景渐进性分层加载技术,突破了终端运行环境的硬件配置瓶颈,为石油石化行业探索CPS积累了宝贵经验。
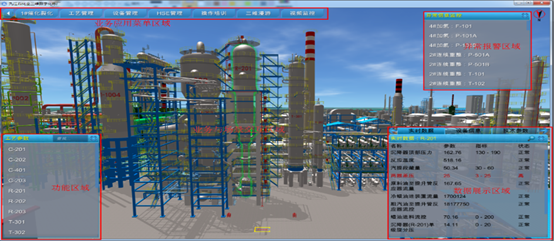
图3 九江石化数字化炼厂平台
(五)实现HSE管控实时可视。通过施工作业线上提前备案、监控信息公开展示,实现“源头把关、过程控制、各方监督、闭环管理”。建立“集中接警、同时响应、专业处置、部门联动、快速反应、信息共享”的调度指挥模式,提高事故响应速度。集成各类环境监测数据,实现环保管理可视化、一体化,异常情况及时处置、闭环管理。
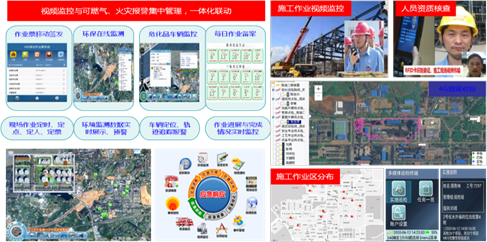
图4 九江石化智能工厂HSE管理
二、实施成效
数字化转型、智能化发展助推企业结构调整和两化深度融合,设备自动化控制率95%,生产数据自动采集率95%以上,运行成本减低22.5%,能耗降低2%,软硬件国产化率达到95%,有效提高企业核心竞争力。“十三五”期间,企业经营业绩持续提升,累计盈利57亿元,年上缴税费均超100亿元。2015年,入选工信部智能制造试点示范企业;2017年,入选工信部首批“两化融合管理体系贯标示范企业”和第一批绿色工厂示范企业;2019年,入选国家智能制造标杆企业。
评论
加载更多