中国高铁是“引进、消化吸收、再创新”的代表作,实施转向架智能制造项目是全新的课题。在没有成熟经验的情况下,中车青岛四方机车车辆股份有限公司(以下简称中车青岛四方)以高速动车组核心部件——转向架车间为实施载体,以关键制造环节智能化为核心,以网络互联为支撑,研发适用于轨道交通装备行业的先进制造技术和装备,实现了高速动车组转向架的智能制造。智慧四方2025愿景如图1所示。
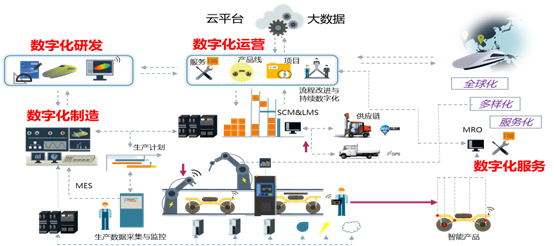
图1 智慧四方2025愿景
实施路径
一、应用大型高档数控机床和重载机器人,提升关键零部件制造水平。为解决传统制造模式下转向架关键零部件—构架和轮轴产品质量一致性差、制造成本高等问题,中车青岛四方通过分析主要工艺流程,对关键工序进行了智能化改造。通过研发自动组焊、打磨、加工、喷涂、人机交互、条码技术、自动异常监控等工艺,实现构架和轮轴的自动化上下料、加工、焊接、喷涂。在轴承压装、转向架装配工序,研制应用精密重载装配机器人、六轴搬运机器人,攻克了机器人吊装与精准移送、部件自寻位精确定位、自动检测与调整等难题,实现了基于机器人的零部件精准自动装配。
二、研发智能传感与控制装备,提高关键装备利用率。为了降低构架焊缝打磨、构架清洗、轴承压装等工序的制造成本,改善作业环境,中车青岛四方研制了180多种智能传感与控制装备,通过智能传感与控制装备替代人工完成复杂的生产作业。为了提高构架加工设备利用率,将数控龙门加工中心、检测设备联网集成,应用RFID实现构架型号自动识别,研发数据采集与控制系统控制数控程序自动下载及删除,工作台自动交换、设备自动启停,实时监测主轴负载,出现异常实时报警,实现了构架加工一人多机控制。
三、研制智能检测与装配装备,全面提升关键工序的效率和质量。为了解决装配和检测工序工作量大、检测结果易受测量人员技能水平影响的问题,中车青岛四方开展了智能检测及装配装备的研制。通过智能装备集成视觉识别技术,轴承检测、转向架落成工序实现轴承自动抓取、转向架自动落成,生产效率提高约10%;基于传感器、工业网络,转向架螺栓扭矩、齿轮箱轴承温度、转向架关键尺寸检测等工序实现了检测结果在线实时监控、系统自动防错技术的全面应用,切实提升产品质量保障能力。轴承检测工序采用激光测试、视觉识别、振动频谱和大数据分析技术,配合智能装备应用,改变了传统人工检测、人工识别缺陷、人工装配方式。
实施成效
中车青岛四方针对实施智能制造的主要任务,分重点、分层次、分环节、由上向下地进行顶层设计,初步建成了转向架智能制造工厂,生产效率提升22.5%,产品研制周期缩短37.16%,产品不良率降低33%,运营成本降低23.8%,能源利用率提升10%。2019年,入选国家智能制造标杆企业。
评论
加载更多