巨石集团有限公司(以下简称“巨石集团”)依托智能制造创新驱动,引领玻璃纤维行业转型升级和高质量发展,确立了以“管控一体化、生产制造智能化、IT服务智慧化”为基础的信息化建设体系。创新应用核心装备、工艺流程和空间布局的数字化建模,突破了高熔化率窑炉的智能化控制、物流调度系统智能化、拉丝设备智能化升级、玻纤产品自动包装物流等关键技术。建成了玻璃纤维工业大数据中心,实现了传统产业向数字化、网络化、智能化发展,在效率、质量、成本取得显著效果。
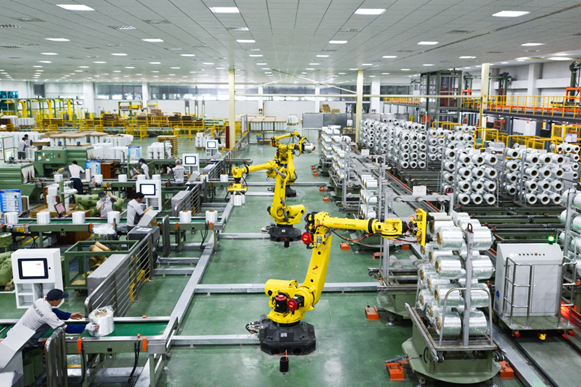
实施路径
一、依托顶层设计,构建智能制造技术架构。巨石玻璃纤维数字化工厂项目以二分厂202线为样板线,以“部署MES系统框架”、“多系统深度集成”、“大数据深入应用”三个智能制造阶段为顶层设计思路建设,从计划源头、过程协同、设备底层、资源优化、质量控制、决策支持、持续优化等七个方面着手实现“七维”智能制造,这七个方面涵盖了工业生产、经营的七个重要环节,实现全面的精细化、精准化、自动化、信息化、智能化管理与控制,通过底层设备的互联互通、基于大数据分析的决策支持、可视化展现等技术手段,实现生产准备过程中的透明化协同管理、生产设备智能化的互联互通、智能化的生产资源管理、智能化的决策支持、3D建模及仿真优化,从而全方位达到智能化的管理与控制。
二、研发玻璃纤维生产核心技术装备及系统。巨石集团结合自身玻璃纤维生产经验,配合生产线结构及生产工艺,自主设计并建设了“智能化物流输送线”、“智能控制高熔化率窑炉”、“智能配料系统”等一系列智能制造核心装备,均为行业内首创,这些智能化设备以及生产线与MES、ERP等应用软件深度融合,并通过智能传感技术及遍布全厂的工业物联网络,实时采集生产过程、环境、能源、设备等信息,实现人、机、设备的互联和集成,打造工业物联智能化工厂的精益协同制造过程。
三、发挥头部企业优势,开展全产业链上下游协同模式。身为玻璃纤维行业的头部企业,巨石集团一直致力于探索如何利用自身优势,促进上下游企业形成资源的流动和信息的共享,共同打造合作、开放、共赢的资源互通平台,促进全产业链的融合发展。通过SRM系统与上游核心大型工艺商开展系统对接,实现采购需求的数字化对接,采购进度实时可见,采购及时率动态跟踪,物资到货实时推送,同时配合基于国产商用密码的电子签章技术,实现采购合同的电子化,显著提高了双方的运营效率,尤其是在疫情后的复工复产期间,优势凸显;向下与典型客户实现产品数据对接,客户可直接扫描产品包装上的二维码,即可查看该产品的批次、型号、质量等相关信息,并且形成相关标准API接口,后续可支持客户不断接入。同时与物流公司、海关系统的数据打通,实现了物流信息实时传输,报关数据精准发送,均极大的提高了业务的快速相应能力。
四、建立基于大数据的全流程工业数据中心。巨石玻璃纤维工业大数据中心,是一个覆盖整个集团生产运营监控平台,通过对生产各工序(窑炉、拉丝、化工、物流线、烘箱、立体库、络纱、短切、检装、制毡、织布)的实时采集数据进行抽取、清洗、聚类、挖掘等处理,并通过各类图表、驾驶舱等方式,形象展示企业生产、运营的关键指标,并可以对异常关键指标预警和进一步分析。
实施成效
巨石集团智能制造生产线的建设包含了一系列先进的智能化新型装备的研制和应用,信息化和大数据分析等新一代信息技术的应用都是创新型的应用,形成了以网络化、数字化等新技术为基础,面向订单的高效生产新模式,支撑玻璃纤维企业运营和管理模式变革,对玻璃纤维两化深度融合发展起到引领和示范作用。
在生产运营方面实现五大综合指标:实现生产效率提高45.04%,生产成本降低20.37%,产品研发周期缩短48.15%,产品不良率降低21.88%,能源利用率提高24.25%。2019年,入选国家智能制造标杆企业。
评论
加载更多