青岛海尔特种制冷电器有限公司(简称:中德冰箱互联工厂)主要生产超大型,超高端冰箱产品。以灯塔工厂标准建造,将设计、研发、采购、制造、模块商全流程并联,探索智能制造互联工厂新模式,以用户为中心,由大规模制造向大规模个性化定制转型,利用COSMOPlat工业互联网平台赋能,围绕冰箱的制造全流程,建设信息化、数字化集成系统,实现了用户定制直达工厂、订单自动匹配和准时交付、生产全流程追溯可视、产品质量实时监控和产品性能的分析优化,有效提升了用户最佳体验、产品品质和生产效率,智能制造综合应用效果显著。
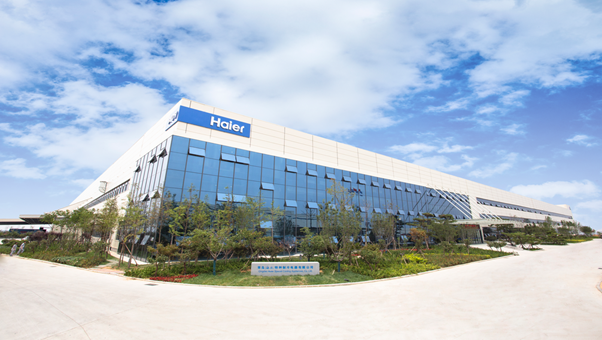
实施路径:
一、互联工厂整体规划。中德冰箱互联工厂根据模块化制造原则进行设计,共分为两个厂房,一号厂房主要用于冰箱箱体生产及箱门体配套。二号厂房主要规划用于箱体内胆成型和门体的生产。工厂布局设计前期采用BIM模型,提前模拟了设备及能源配套等配合问题,一个流设计原则减少了库存和工序之间周转,提升了产品品质和生产效率。工厂内搭建了APS、MES等数字化系统,并与集团级应用系统如PLM、ERP、MDM等集成形成智能运营决策平台(BI),实现了智能装备互联互通、应用系统无缝集成、数据可视及分析,全流程全维度上下游业务互联互通。
二、建设智能化生产线体。自动、柔性、智能化的高端线体是满足用户最佳体验的基础,也是中德冰箱互联工厂的特点之一。工厂从冰箱的模块制造及检测设备、整机装配及检测设备、模块的输送设备三方面研发和应用了全球家电行业最领先的高端线体。
三、建立完善的智能制造体系。基于核心流程的指标体系,搭建全流程最具竞争力智能制造运营团队。建立数据分析标准及管理准则,对管理智能制造升级改善点进行PDCA闭环,持续优化,实现工厂智能制造模式持续升级。
四、实现数字化运营管理模式。利用智能设备互联互通、应用系统无缝集成、数据可视及分析,建立中德冰箱互联工厂数据运营决策平台,营造工厂数据文化、用数据说话;通过数据发现问题,找到业务/IT/流程的改善点,闭环优化。以数字化作为支撑,实现了工厂智能制造模式持续升级。中德冰箱共实施9大智能制造系统达成Q、D、C、P、S、M目标引领,通过大数据分析平台的预警报警信息传至智慧运营系统进行跟踪闭环,达成智能化运营模式,实现由传统经营管理向数字化经营管理转型升级,建立了完善的智能制造体系,智能制造竞争力持续迭代升级
实施成效:
中德冰箱互联工厂投产后,企业生产效率提高15%以上,物流效率提升30%,部分工序用人节省接近80%,企业综合运营成本降低22.5%,缩短产品升级周期31.6%,降低企业不良品率25.4%,OEE 提升19%,平均每年增加利润20%。中德冰箱互联工厂自建设以来,获得首批国家智能制造标杆企业称号,获得工业4.0引领园区奖,获得金长城智慧制造工厂称号,其在高端制造,引领技术和信息化智能化方案的创新实践在业内已得到广泛认可,引导白电企业关注和应用智能化技术,有效的帮助解决行业现有问题,对冰箱行业产生良好的示范效应,更好的满足冰箱行业快速发展的需求,进一步提升我国高端冰箱制造企业国际竞争力,促进行业发展。2019年,入选国家智能制造标杆企业。
评论
加载更多