湖南科力远高技术集团有限公司(以下简称“科力远”)自主研发智能制造体系工程系统平台,并应用于动力电池行业,提出了覆盖产品需求、设计、制造、运行、维护全生命周期,以及产品、用户、生产线、任务场景和关联系统等全体系、全场景的智能制造系统解决方案,深度实践动力电池行业的“智造”之路。通过研发、规划、排程、现场管理、仓储物流管理、产品服务等全流程智能化赋能,有效缩短动力电池产品研制周期、降低运营成本、提高生产效率、提升产品质量、降低资源消耗。
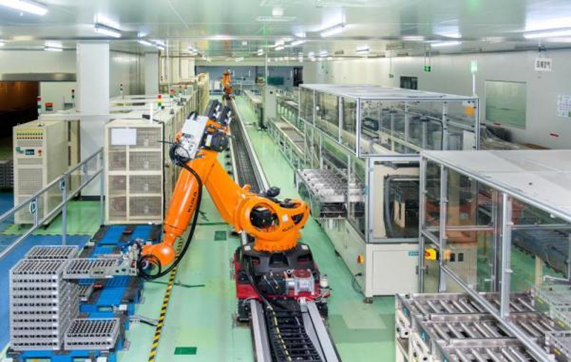
图1 基于体系工程的科霸动力电池智能工厂实景
一、实施路径
(一)总体规划。科力远智能工厂建设主要涵盖智能设计、智能经营、智能生产(包含MES、控制系统、智能检测与装配装备、智能物流和仓储)和智能服务四大主体,主要包括智能化的电池极板制造、电池装配、电池化成及仓储物流设备,并在智能保障体系的基础上通过数据集成和系统集成构建出动力电池智能工厂。
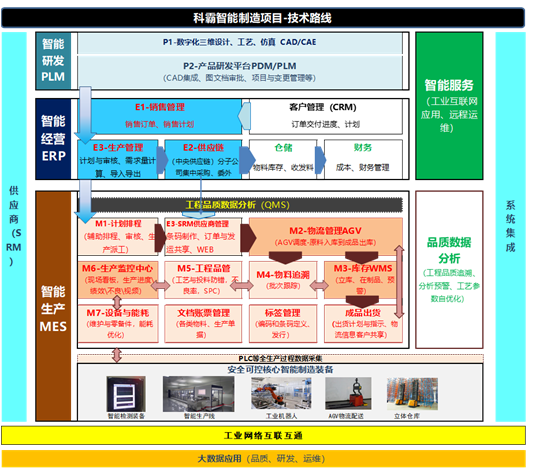
图2 智能工厂项目技术路线图
(二)实施目标与策略。通过应用工业机器人、智能传感与控制装备、智能检测与装配装备、智能物流与仓储装备,实现产品生命周期中的设计、制造、装配、物流等环节的数据互通,从而缩短产品设计到生产的转化时间,实现产品整个生命周期系统高效和透明化管理。
(三)实施内容。基于体系工程的智能制造建设,涉及基础设施改造、产品设计效率提升、生产规划能力提升、生产制造管控、信息系统融合、生产监控与指挥、产品售后服务提升等方面的内容。通过工业以太网、工业无线网通讯以及构建信息安全来实现工业网络互联互通,实现基础设施改造提升;通过融合三维设计软件、三维仿真软件和虚拟验证实现智能研发,提升产品设计效率;通过数字孪生平台实现全要素智能规划,提升生产规划的推演预测;通过建设MES系统、融合智能管理进行高效管控;通过建立标准化的接口平台,统一接口方式和接口管理平台实现ERP、MES、PLM系统集成实现信息系统融合;通过大数据系统技术建立生产监控与指挥中心;通过在交付物理产品给客户时,也同时提供该物理产品对应的数字孪生体给售后运维部门用于远程监控物理产品的实时工况来实现智能服务提升产品售后服务能力。
二、实施成效
通过智能工厂项目,科力远建设了电池极片、车载电池的智能化工厂,助力公司快速发展。智能化建设3年来,实现生产效率提高33.2%,运营成本降低24.1%,产品不良品率降低82.1%,产品研制周期缩短37.2%,单位产值能耗降低24%。客户满意度由91%提升到98%,产品的交付期缩短16天,有效提升了企业的竞争实力和快速应变能力。
评论
加载更多