润滑的的经济效益
合理润滑不只是投入,而是能给企业带来可观的经济效益,由于合理润滑投资回报率高,日本也称之为“润滑经济”。下面列举合理润滑产生经济效益的典型案例。
1966年,乔斯特(JOST)教授受英国政府指派,对摩擦的影响进行统计分析。乔斯特经过调查后发表了一份关于摩擦现象对英国社会影响的研究报告,即著名的《乔斯特报告》。该报告对世界摩擦学的研究和发展起到了重要作用,引起了世界各国对摩擦学的高度重视。该报告中指出,摩擦每年为英国造成巨大的经济损失,如果利用现有的摩擦学理论和润滑技术,科学地控制摩擦,英国每年可节省5.15亿英镑:少维修和更新2.3亿英镑,占节省的44.66%;减少机器故障1.15亿英镑,占节省的22.33%;延长机器寿命1亿英镑,占节省的19.42%;减少摩擦、磨损0.28亿英镑,占节省的5.44%;节约投资0.22亿英镑,占节省的4.27%;节约润滑剂0.1亿英镑,占节省的1.94%;节省人力0.1亿英镑,占节省的1.94%。
1970年乔斯特应邀来我国进行摩擦方面的研究,他指出,如果科学地控制摩擦,中国每年可节省400亿人民币。故改善润滑、控制摩擦,就能为我们带来巨大的经济利益。
中国工程院咨询研究项目《摩擦学科学及工程应用现状与发展战略研究》调查显示,2006年全国消耗在摩擦、磨损和润滑方面的资金估计为9500亿元,其中如果正确运用摩擦学知识可以节省人民币估计可达到3270亿元,占国内生产总值GDP的1.55%。
美国机械工程学会在《依靠摩擦润滑节能策略》一书中提出,美国每年从润滑方面获得的经济效益达6000亿美元。1986年,中国的《全国摩擦学工业应用调查报告》指出,根据对我国冶金、石油、煤炭、铁道运输、机械五大行业的调查,经过初步统计和测算,应用已有的摩擦学知识,每年可以节约37.8亿元左右,约占生产总值(5个行业1984年的可计算部分)的2.5%。
润滑油的支出仅是设备维修费用的2%~3%。实践证明,设备出厂后的运转寿命绝大程度取决于润滑条件。80%的零件损坏是由于异常磨损引起的,60%的设备故障由于不良润滑引起。中国每1000美元产值消耗一次性能源(折合石油)为日本的5.6倍,电力为日本的2.77倍,润滑油耗量为日本的3.79倍。
润滑管理的机会成本
加强润滑管理在提高设备可靠性或降低运行风险方面有重要的价值贡献。通过科学的润滑管理,采取正确的解决办法,消除问题的根源,可以避免停机损失的发生,以下是相关的成本构成。
√ 修理成本:某台设备每年出N次故障,可以估计出为使设备恢复正常而付出的配件和人工成本。
√ 停机成本:如果一台关键设备停止运转,就会对上下游生产产生影响,可以估计出一台机器出故障时的典型停机成本并乘以生产时间损失的平均时长。
√ 润滑剂成本:改善润滑管理能降低润滑产品的消耗,对节省的估算应包含润滑剂成本、人工和处置成本。
√ 能耗成本:通常改善润滑管理和油品品质会降低摩擦损耗,通过借助某些方法来比较改变之前和之后的正常作业能耗,能够有效估算出这些节省量。
√ 品质成本:一般而言,通过对润滑油品进行妥善管理,可减少百分之一的缺陷。在机加工、轧制和铸造等领域应用更明显,因为液压控制的精度会受到润滑油品质的影响。
√ 产量成本:在某些情况下,实现了合理润滑的设备产出量更高。例如,润滑不良或油品污染都可能减少设备的运行时间,从而降低产量或影响生产。在油气田领域也是如此,从长远而言运转良好的设备能生产出品质更高的产品或产量更高。
√ 基于风险的成本:安全风险、环境保护等基于风险的成本应当在实际生产上纳入评估中。
油脂浪费严重
在实际应用过程中,润滑脂浪费现象较为严重。因为客户使用的油脂一般是桶装油脂,所以难免存在取用的问题。在此引用《经济师》2011年第5期文章《润滑油脂选用浪费与发展低碳经济探析》章节:“ 现将20公斤铁桶润滑脂进厂后的种种浪费现象剖析如下:
第一步:进入工厂仓储中心的润滑油脂下发时因容器壁粘粘损失在2公斤以上。
第二步:各车间领取后由于保管不当,有时表面落些灰尘杂物等要报废一些,加上容器壁粘粘损失1公斤左右。
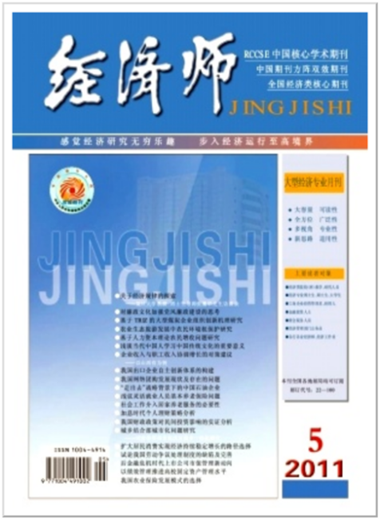
第三步:一般维修师傅到车间领用润滑脂时随便找一个小铁皮碗或者一张纸之类,等到2/3脂加到轴承之后,其1/3留在钳桌台上,时间一长沾满灰尘后随手丢入垃圾箱里,这样有30%以上的润滑油脂被浪费。
第四步:由于轴承壳内润滑脂真正起作用的的仅需1/3~1/2,有时因脂加得太多,内摩擦过大散热差造成轴承温升太高,因此加在轴承内润滑脂平时50%也被浪费掉。
这样一桶润滑油最后实际利用率绝不会超过50%。” 随着管理水平的提高,现在的油脂浪费现象有所改善,但是上面提到的问题仍普遍存在。
科学润滑事半功倍
如何实现科学润滑,以取得经济效益?如果想进一步完善设备维护管理流程,润滑管理审核至关重要。但是,、需要审核什么内容呢?例如:员工和生产机器有哪些危险情况、是否有任何难以接近的关键润滑点、当前使用的工具是否缺乏、维修人员是否受过良好的教育、您的润滑过程是否适合您的维护组织等等。而审核是为了更好地完成KPI,例如:减少20% 的润滑油消耗、将齿轮预算减少30%、将计划外机器停机减少10%、提高员工安全性……
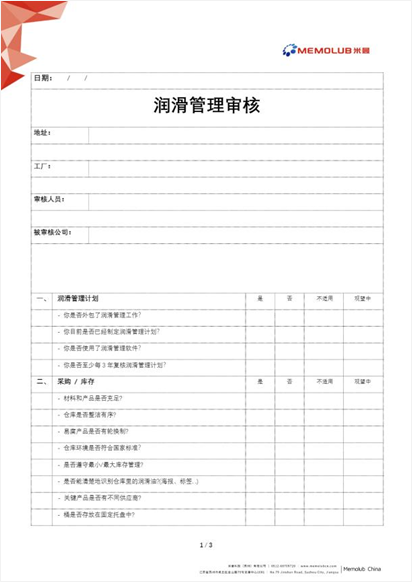
通过对润滑管理的全面审核能有效发掘可改进的地方,完善管理流程,控制生产成本。米曼在润滑管理方面有超过30年的经验,联系我们可免费领取润滑管理审核模板(中/英文),还有免费噪音及温度测试,以及润滑培训等。
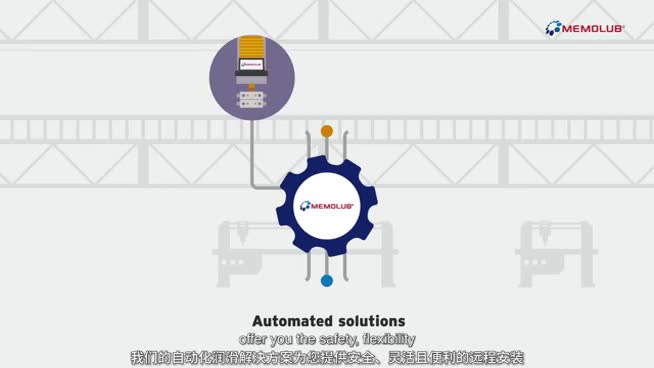
评论 0
正在获取数据......