上汽通用五菱汽车股份有限公司作为汽车设计研发、制造、销售综合性的制造业企业,拥有5个生产工厂基地,每个基地基本都有冲压、车身焊接、涂装、总装和发动机车间。平均每个基地拥有100~160套PLC控制系统,生产线设备都是由各种复杂的工艺设备、输送设备、自动化设备(机器人、AGV、NC等等)以及工装夹具等设备组成,这些设备单元由PLC通过现场总线与各种控制执行单元组成生产线控制系统。以控制器为大脑核心的控制系统相当于整个生产线的神经网络和指挥执行系统,是提升自动化及生产效率的重要手段。
目前公司设备控制系统是以Rockwell公司的ControlLogix & GuardLogix控制器为核心组成的,整个控制系统建立在GM全球ME控制系统架构基础上:GCCL全球元器件采购选型清单、GCCH&GCCB全球控制图纸和制作标准、GCCS程序设计规范、GDHS全球环境健康卫生安全体系和PMC(工艺生产过程管理控制)、AVI(白车身跟踪管理)、ANDON(生产响应拉动及分析)以及智能防错等控制系统。
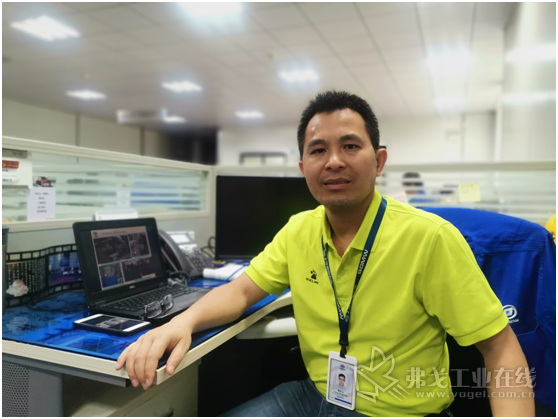
上汽通用五菱汽车股份有限公司技术中心
自动化部控制系统工程科高级经理 龚兴元
采用优质的PLC控制器,能够应对整个复杂的自动化设备、工艺质量等生产数据采集及分析,实时掌控生产运行状态,确保生产安全及效率和产品品质。从生产运维来说,控制系统的标准化,可以使得设备维护人员技能统一、简单化,同时备品备件统一,可以确保设备问题快速响应。目前,汽车行业大多采用安全PLC,和传统的PLC相比,安全PLC可以在根本上实现安全采集和输出。同时在通信方面,从传统的点对点的采集发展到现场总线普及,对现场的布线、故障处理、传输速度上都带来很大的优化和便利。
随自动化提升,生产人员逐步减少,生产管理需要增加设备管理的比重,来确保生产效率。随着用户对汽车的个性化要求越来越多,生产柔性越来越高,综合性的数据采集,精准的设备及生产实时状态透明化和统计趋势分析同样势在必行。我们开始改进原来的控制系统,进行智能化升级,采集更多的设备、质量、物流、调度以及能源等数据,进行统计分析。把自动化生产线在线无损切换频次、综合效率、设备及生产数据的综合分析决策能力,作为生产线智能程度的重要考评指标之一。
自动化建设成本高、周期长、生产效率低是目前的痛点。对技改项目建设周期和质量,以及生产线运行后的效率追求,才能够确保产品早日推向市场,以及综合制造成本利润最大化。针对此,我们开始局部尝试性加强数字化工厂建设和生产线虚拟化运行仿真及虚拟集成调试,对现场实施来说,确保设计一次性准确率100%,直接压缩现场建设周期和风险。
当前,控制器市场被不断细分,我认为控制器市场的差异性需求主要这么几个层面:第一层面是针对系统复杂程度(自动化)划分:如,小型系统、中型系统、大型系统,这是系统点数需求层面的差异性;第二个层面是安全需求的差异:不同的生产线环境安全需求不同,如安全PLC通过安全总线结合安全模块,集成安全设施能够使系统达到一定的安全级别,减少复杂的硬接线来确保安全;第三个层面是离散行业和流程行业的差异性:为了应付自动化升级,控制器市场也一直在做创新,比如AB的软件已经从传统的Logix 5000,升级到了Studio 5000,Siemens的软件已经从Step7演变到了如今的博途系列等,功能越来越强大,实现了全集成自动化更优功能。第四个层面是新技术带来的便利性和差异性:高端PLC的通讯接口统一化,未来或将更广泛地采用无线技术。由于无线通讯技术的突破,可靠性和安全性会得到极大的提升,加上芯片技术成熟和价格逐步低廉,机电一体化设备会越来越多,内嵌处理器的智能型传感器也会越来越多。整个控制系统的现场集成,将来更多的是模块单元化配置这种标准化作业,而不是在现场进行大量的安装以及调整调试非标工作。
随着5G技术的落地,本身具有独立处理和通信能力的传感器等元器件可以实现互联互通,数据信息所面临的安全问题也日益突出。对工控系统来说,控制器本身的安全排在第一位,要保证其不被无故或恶意篡改,否则会导致严重的人身伤害、设备损坏、或环境污染等事故;其次是控制系统中关键质量和生产数据信息的安全,这些数据会对产品质量造成直接影响。如何解决这些问题,具体还是需要看整个控制系统与公司内外IT系统关联程度来确定,可以考虑几种管理方法:
● 物理隔离,控制系统网络独立,不与任何其他网络链接;特别是车身焊接车间,采用大量的光栅、激光扫描、安全门等安全设施来确保人身操作和日常维保安全。
● 加强交换机IP地址管理,采用车间级网络系统应通过网管型交换机进行地址分配,:实现车间之间的网络隔离,这样就可以最终实现控制网与MES网隔离,车间之间网路隔离,当局部的网络病毒侵入、传播时可以控制在很小的范围内,不至于影响到其他网络;
● 密码权限管理,PLC设置层级安全密码授权管理,以及控制柜人工设钥管理,限制人员随意可以访问并修改程序和参数;加强维护维修以及技改人员PC应用授权和监控。
● 引入第三方软件管理,对任何异常侵入以及修改,都及时发出提醒和完整记录修改日志;
未来,我们更希望控制器产品使用安全、操作简单、故障率低,维护方便;有统一的通讯协议、健全的程序库,编程更加简单、更加人性化。同时在多处理器架构的高性能、通讯及控制模块切换、即插即用、设备诊断专家化、可视化界面友好、版本固件升级便捷等方便进行提升与改进。我们可以推测未来PLC会达到两级分化的状态,一部分更为集中,形成控制平台,可导入高级语言开发程序模块单元,甚至标准设备控制程序模块商品化、适应数字工厂和虚拟运行嵌套;另一部分更为小型离散化,网络拓展更强、数据处理能力、控制元器件智能化、机电设备集成化。
评论 0
正在获取数据......