贝加莱的 ACOPOStrak 输送系统用于圆柱电池的X射线检测系统。该系统具有极高的柔性、跨线或并行操作,以实现生产的连续流,将经济高效的操作与令人印象深刻的检测性能结合在一起。
电动汽车约1/3成本来自电池。车辆的续航能力取决于电池容量,这对大多数买家来说仍然是最重要的特征。电池的质量和可靠性对安全性和驾驶性能有直接影响。因此,在生产过程中对电池进行100%的检测至关重要。X射线检测已成为电池在线检测的常用方法。
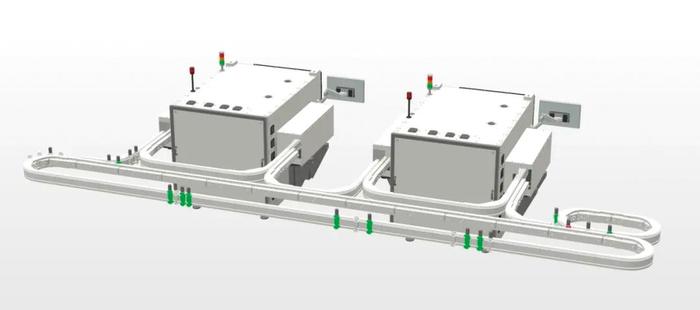
ACOPOStrak:两个检测系统可以以极高的灵活性集成到工艺过程中——电子换向器使之成为可能
每分钟进行175个圆柱的X射线检测
来自汉诺威的Exacom有限公司专门从事方形和圆柱电池单元的检测。该公司向一家知名电动汽车制造商的超级工厂提供了用于圆柱电X射线检测的iXcell系统。为了达到每分钟约 175 个电池片的检测速度,该系统采用了贝加莱工业自动化的ACOPOStrak输送系统。
Exacom 公司总经理Hagen Berger解释道:“基本上X射线检测有两个决定性因素。首先,我们必须掌握图像采集技术,同时我们还需要一个合适的输送系统。”
整个电池生产设施将 iXcell 技术的 X 射线检测完全集成到生产线中,在关键生产步骤中对每个电池进行检测,如果检测不合格,则立即将其取出。这意味着有缺陷的电池不会在整个流程中被拖到生产线末端才被弹出,从而造成产量、原材料和能源的损失。
同时,iXcell工作站的在线集成还意味着X射线系统必须与生产流程保持同步,不能成为瓶颈。在电池生产过程中,每分钟有150~175个电池单元离开自动卷绕机,并且每个电池单元都必须在约 340 ms的时间窗口内通过所有检测。
Hagen Berger解释道:“在检测过程中,载有电池单元的单个输送小车必须绝对静止。停止后的每次振动都会延长检测周期。贝加莱的专家配置了输送系统控制器,使电池在 X 射线站中以最大可能的减速和预定义的运动曲线减速,并最大限度地抑制振动。”
iXcell:X 射线检测系统专为满足圆形电池生产的要求而设计
Berger将ACOPOStrak系统布局几乎无限的灵活性视为一个独特的卖点:“与传统的单轨系统相比,贝加莱在整个系统的设计上提供了高度的灵活性,特别是在连接不同的工艺步骤时。ACOPOStrak的变轨技术使我们能够轻松通过旁路轨道分离出有缺陷的电池,设置并行产品流,或者在必要时将工艺流程引导至特定工位,而无需中断生产(例如在需要维修时)。据我所知,没有其他制造商可以实现这一点。”
Berger举例说明了这在实践中的意义:“ACOPOStrak 的设计是我们能够从超级工厂的四台卷绕机中拾取圆柱电池,并将它们送入两个 X 射线系统。由于路径灵活,我们甚至可以在必要时移动到旋转工站,从而允许带有旋转 90°的测试样本的单元第二次通过系统。”
借助数字孪生 更快实现目标
在数字仿真的帮助下,在很短的时间内测试并确定了系统设计和测试样品进出 X 射线系统的位置。这还包括找到了合适的生产线布局,以优化电池测试样本的处理,包括缓冲、放电和物料流动。Berger满意地总结道:“这加快了开发速度,减少了试验次数和错误,使我们能够在开发过程中尽早确定电池和载体的放置方式。”
评论 0
正在获取数据......