你在生活中一定有过这样的经历——当手指无意间碰到灼热的物体时会立即缩回。这是神经系统形成的反射在保护我们不受伤害。但你可能没有想到的是,无论是遨游太空的航天飞船,还是深入海底的载人潜水器,它们的“身体”里也都有一套自己的“神经系统”。而看似不起眼的连接器则好比“神经系统”中的“神经元”,肩负着数据信号传输的重要使命。
连接器是一种典型的“多品种、小批量、定制化”产品。在中国贵阳,有这样一个智能制造车间,其产线足以支持超过10万种连接器产品的柔性生产,让“工业4.0”从愿景变为现实。这间智能车间的主人,正是中国航天科工集团(航天科工)第十研究院下属上市公司,国内集科研、生产于一体的电子元器件骨干企业——贵州航天电器股份有限公司(航天电器)。
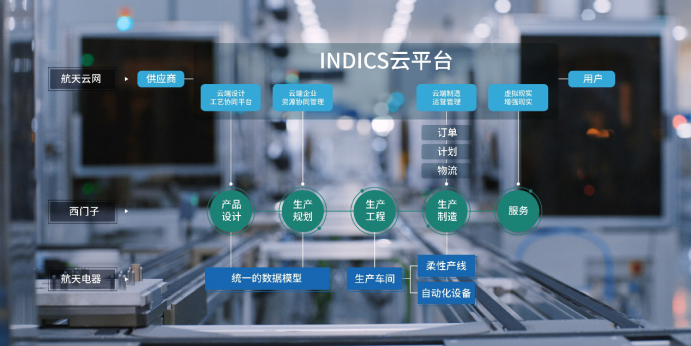
图1 精密电子元器件行业全球首个基于工业互联网平台,具有云制造能力的智能制造样板间
出于提高质量、降低成本和提升效率的内生动力,早在2000年,航天电器就在自动化领域展开探索。“然而,自动化解决不了多品种、小批量产品的柔性化生产问题。随着公司发展速度进一步加快,我们开始朝着智能制造的方向迈进。”航天电器董事长陈振宇表示。
2016年,在智能制造的浪潮之下,航天科工和西门子达成合作,致力于探索一条适合中国企业自身发展的转型升级之路。自上而下和自下而上的两股力量在智能制造的节点上正式交汇,由此诞生了精密电子元器件行业全球首个基于工业互联网平台,具有云制造能力的智能制造示范项目——航天电器智能制造样板间。
该项目由航天科工下属企业航天电器、航天云网和西门子共同建设。这是航天电器倾心打造的基于工业互联网平台具有云制造能力的智能制造样板间,也是三方在离散行业全球第一个最完整的数字化企业项目。该项目分别位列2017年首批中德合作——中德智能制造试点示范项目和2018年中国工信部智能制造试点示范项目。
洞悉需求,有的放矢
2016年11月1日,航天云网、西门子与航天电器正式签署协议,为该智能制造样板间项目提供咨询和技术支持。经过各方的详细沟通和认真梳理,该项目于2017年3月正式启动实施,正是因为充分的前期咨询和设计,才避免了在后期项目实施阶段可能出现的重大问题。
作为电路与电路之间沟通的“神经元”,连接器随着应用对象、频率、功率和应用环境的不同而具有千变万化的形式和结构,所以航天电器当时面临的最大挑战就是如何高效地实现产品的柔性化生产。
航天电器智能制造专业总师刘林琳表示:“我们每个月会收到超过6000个批次的订单,其中70%的批量都在九件以下。”航天电器传统的自动化解决方案很难满足如此高度定制化的需求。
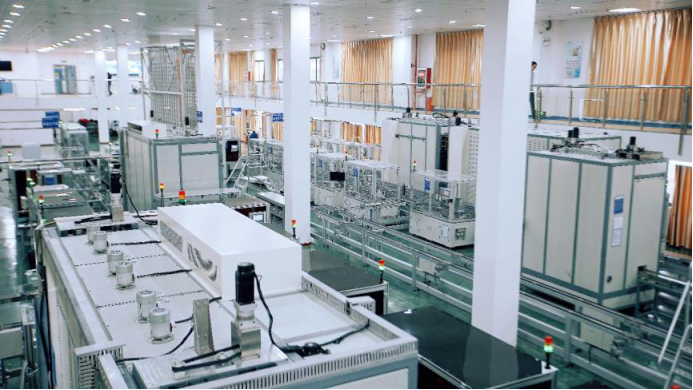
图2 智能制造样板间项目架构示意图
三大集成,价值贯通
航天云网构建了工业互联网平台,展示了云制造支持的能力;西门子凭借数字化企业整体解决方案,将智能化贯穿全生命周期;航天电器搭建了样板间整体,实现了网络化智能装备生产线,具有柔性装配、智能精密检测等功能。三方共同构建了从订单到设备,从研发到服务,从供应商到客户的三大集成体系,实现了数据驱动的多品种、小批量柔性混线生产。通过样板间项目,航天电器实现了内部所有信息化和自动化系统之间的纵向集成,能快速响应客户需求,及时完成产品交付,并实现生产全流程的数据透明和可追溯。
具体来说,来自市场的订单将通过ERP(企业资源计划)系统进行统一的管理和下发。ERP在接收订单之后,航天云网基于INDICS云平台的CRP(云端企业资源协同管理)系统能够根据有限产能进行智能排产。接着,生产计划被进一步推送至MOM(制造运营管理)系统,MOM负责实施具体的生产任务,并在整个生产过程中把控产品质量、记录生产数据。其中,西门子TIA(全集成自动化)和航天电器的自动化设备是实现智能制造的基石。在样板间中,MOM和TIA能够实现数据的双向通信,借助于智能制造装备,使产品的柔性化生产成为可能。车间里,产品和部件在产线上流转;办公室里,企业管理人员足不出户,戴上VR眼镜,即可身临其境地实时看到产线生产的实际情况。
航天云网天智公司副总经理庄鑫表示:“在以往的业务流程中,数据虽然记录在各种系统中,但是它们静静地躺在数据库里,其价值也仅仅是追根溯源。而现在,通过航天云网的CMOM(云端制造运营管理)工业大数据分析系统,我们可以充分挖掘数据价值。”
为了帮助航天电器高效应对来自市场的多样化订单,西门子基于其数据协同平台Teamcenter为航天电器搭建了一套可配置的超级BOM(物料清单)。BOM是描述企业产品组成的技术文件,它表明了产品的总装件、分装件、组件、部件、零件和原材料之间的结构关系以及所需的数量。超级BOM把多种产品的BOM组合在一起,对其进行有效管理。
如果Teamcenter中没有现成的BOM,那么西门子NX设计软件则可以帮助研发人员快速进行产品设计工作。为打破航天电器与客户、供应商之间异构的研发环境带来的局限性,航天云网基于三维数据体系搭建了CPDM(云端设计工艺协同平台)系统,为航天电器的销售、设计工艺人员及外协外购商和客户各方提供了一个统一的协同研发交流环境。在从研发到制造再到服务的持续“进化”过程中,各阶段的BOM数据相辅相成,既基于统一的数据平台Teamcenter实现了良好的协同,又基于CPDM实现了跨系统的沟通。
航天云网基于INDICS云平台的CPDM系统可以助力旗下各子公司之间跨系统进行研发设计和工艺协同。包括设计、工艺及制造在内的产品全生命周期流程中产生的数据都会被统一写入Teamcenter软件中,供不同团队之间进行共享,这非常有利于研发和工艺知识的积累。
另外,用户的体验也会发生翻天覆地的变化。原来,来自市场的订单可能需要航天电器的内部人员手工录入到ERP系统中;未来,用户可以直接在航天云网的云平台上一键下单。
面对如此复杂的项目,三方团队在项目执行过程中难免会遇到严峻挑战。但是无论碰到什么问题,三方的目标始终保持一致,以航天电器董事长陈振宇为代表的领导层甚至亲自组织周例会以动员大家的积极性,努力解决实际存在的问题并规避可能的风险。
相比于原来的自动化生产车间,该智能制造样板间的生产效率预计将提升50%,产品不良率将降低56%,运营成本将降低21%,产品研发周期将缩短30%。
评论 0
没有更多评论了