时间压力越大,节约的时间就越值钱。这在机械工程设计中体现得尤为明显,尤其是在交货期很短的情况下。因此,对于项目经理和设计师来讲寻找节约时间的解决方案至关重要。在机床设备现场施工和调试中最多的时间“浪费”在哪里呢?智能化的解决方案能在哪里消除时间浪费的根源、减少不必要的操作步骤并节约宝贵的时间呢?
节约时间的潜力蕴藏在从设计理念到机床设备装配的每一个步骤之中。本文介绍了智能传感器技术如何帮助用户避免浪费时间、加快项目进展的实例。
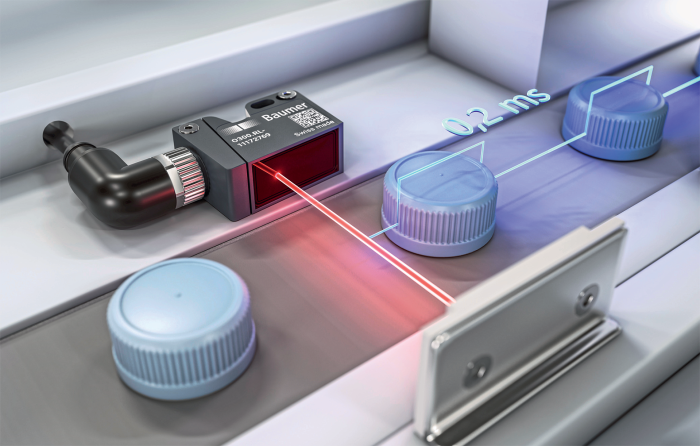
图1 有着准确参考光轴的光学传感器:节约了现场安装时间、简化了安装工作
光束路径是一个错误源
在工程技术领域中,工程师们喜欢用光栅或者光学传感器来识别物体。机床设备中的这些光学探测仪器能够准确、非接触式地探测物体,并且有着非常短的响应时间。为了使这些光学仪器能够按照设计师的设想正常工作、让光学传感器发射出去的探测光准确地达到目标区域,设计师必须解决好以下几个问题:
工程师要在设计阶段就用CAD软件设计好光学传感器光束的正确照射路径。因此他必须选择好光学传感器的照射角度、注明照射精度允许的偏差;
安装光学传感器时要注意其设计是否符合实际情况的要求。除了数据填写和传输过程中可能出现的错误之外,由于生产条件的原因也可能导致数据的允许偏差出现错误或者丢失了部分数据。设计使用的数据与实际情况符合度越高,调整光学传感器使其对准目标的可能性就越小;
在设备上调整光学传感器使其对准目标。光学传感器的安装方法应使其能够准确地对准目标区域。在使用反射光栅时应准确地对准反射器。这些听起来都很简单,但在实践中却要耗费大量的时间。因为在光束准确对准目标物之前往往需要反复调整。
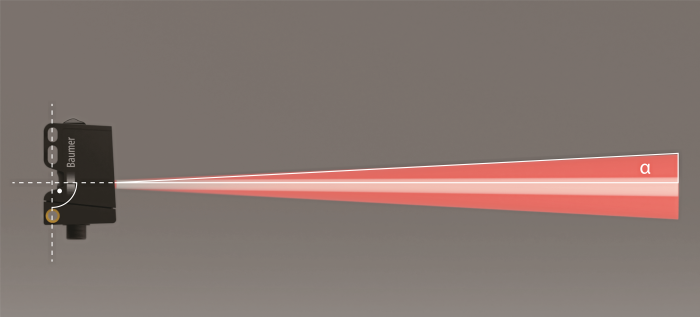
图2 “q Target”原理图:光学传感器的光轴垂直于参考孔,α角的最大角度为1°;图中显示的角度明显大于1°,只为说明问题
参照孔节约设计时间
如果光学传感器的光束路径不是人工手动现场操作的,传感器光束能够按照预定的路径照射,则完成上述三步就会明显缩短光学传感器的调整时间——就像Baumer公司的光学传感器一样。光学传感器发射出去的光束能够准确地通过固定安装的参照孔时,就排除了其他零部件制造时的误差。
一般情况下,一个批次生产出来的光学传感器有着相同的精度,这也就保证了这一批机床设备使用的光学传感器都有着相同的、很短的调整时间。这被称为“q Target”的特性可以在无需精细调整的情况下快速地完成光学传感器的安装任务,也可以轻松地更换光学传感器。
保证了光轴对准目标区域的情况下,现场施工阶段就可以节约时间。Baumer公司设计制造的诸如O200、O300、O500以及OT300和OT500,光学传感器都集成有光束模式的3D-CAD数据。这就让使用这些传感器的工程师们不必再劳心费力地从数据表中查找相关数据了。他们只需简简单单地将Baumer公司提供的数据——光束出口、盲区、包括最大偏差在内的探测范围及接收区域等转移到自己设计的CAD模型中就可以了。
这不仅减少了出现错误的根源,而且也节约了大量的时间。得益于“q Target”能够使CAD模型中的光束可靠地与现实中的光束路径保持一致,这也就确保了从规划设计到设备装配时都可以更加省时省力。简而言之:按设计要求安装的光学传感器无需额外地找正调整。
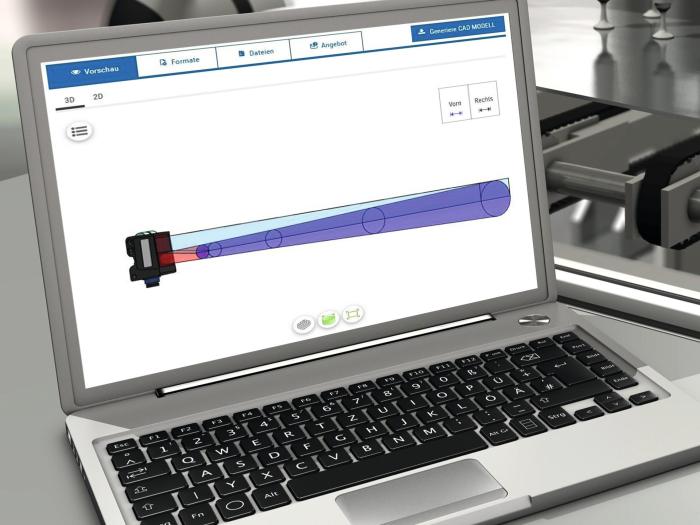
图3 光学传感器的光束数据都集成到3D-CAD数据中
安装和更换时也节约时间
Baumer公司一个实际例子就充分说明了智能化解决方案所节约的时间有多少了:一位来自内部物流领域的客户在物流中心自动分拣设备中安装了14 000个光学传感器。由于传感器光轴采用了“q Target”技术,使这家内部物流客户省去了传感器找正对准的工作量。按每个传感器找正需要5 min计算,所有传感器找正调整时间的总和就是一个相当可观的数字了。
对这家内部物流企业来讲,能够节约这么多的时间也是他们选择O300型反射光栅的重要原因之一。因为“q Target”不仅在设备的安装调试过程中为客户带来了巨大回报,而且在今后的使用操作过程中也会得到丰厚的回报。因为更换受损的光学传感器时不需要对新安装的备件进行调整。此外,Baumer公司不仅生产集成了光束路径的光学传感器,还生产在3D-CAD数据中集成了声波锥的超声波传感器。
利用集成在3D-CAD数据中的光束路径数据和预定义的光轴,Baumer公司为机械设备的高效设计、生产制造和使用操作提供了一个最佳范例。在Baumer公司的One-Box设计理念也实现了很高的使用灵活性,所有的功能原理零部件、光源都是一样的外观形状,但却有着不同的外壳设计:塑料外壳、卫生型外壳和可冲洗外壳。
评论 0
正在获取数据......