发动机生产过程具有工况多样、结构复杂、性能要求高等特点,针对以上特点,为提高发动机多品种大批量的智能制造水平,潍柴动力通过智能制造整体战略布局,构建了较为全面的研发、生产、运维体系。建立了企业级的统一数据中心,信息覆盖度达到92%,实现了集团、分/子公司信息系统和第三方的数据共享。通过应用IRDS智能快速设计系统、PDM产品数据管理系统、WPM工艺设计系统,实现了基于知识库的产品设计和工艺设计。基于自主研发的ECU模块,开发了智能测控及标定系统,实现了发动机数据采集、状态监控、寿命及故障预测等功能,为用户提供了优质的售后服务及增值服务。
实施路径
一、制定总体规划。总体规划选取潍柴动力一号工厂作为智能制造示范场所,利用信息物理融合CPS、云计算、大数据等新一代信息技术,建立以工业通信网络为基础、以装备智能化为核心的智能车间,研发以ECU为核心的系列智能产品;建设全球智能协同云制造平台、智能管理与决策分析平台、智能故障诊断与服务平台,培育以网络协同、柔性敏捷制造、智能服务等为特征的智能制造新模式;探索智能制造新业态,“低成本、高效率、高质量”地满足客户个性化定制需求,为客户创造超预期的价值。
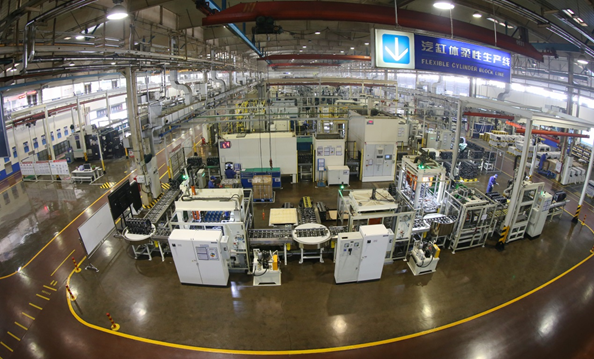
潍柴柔性制造产线
二、产线改造升级。柔性混线生产线改造升级,在既有特定型号刚性生产线的基础上,引入其他型号柴油机的专用拧紧工具、标准工具、工装、工位器具等装备,在加工线、装配线关键工位的装备中嵌入具有可感知、可采集、可传输的智能化嵌入式芯片,使关键工位的装备可实时感知生产线上流转的产品系列,大大提高了发动机柔性制造能力。
三、数据互联互通网络系统建设。为保证工业大数据采集、传输的实时、准确和高效,进而为基于大数据的企业综合管控平台提供数据基础,建设了智能工厂底层装备信息数据采集互联互通网络系统。一是大数据采集及设备互联互通升级建设。研发智能网关设备,通过提供制造业现场生产设备的信息集成与协议转换能力,实现不同设备或者管理控制系统的联通,构建现场通讯协议仓库,提高工业大数据采集和设备互联互通能力。二是工业互联网升级建设。对现有工业互联网进行智能化升级改造,具体包括工业PON网络的建设和架设园区LTE网络等。
四、搭建工业大数据综合分析决策平台。建立企业级统一的大数据存储、建模、分析、决策平台,各业务环节均可在此平台通过大数据和云计算等技术将采集数据进行大数据分析、建模,同时可与现有信息系统的集成应用。
实施成效
通过智能制造的实施,企业各项指标均有明显提升,装备联网率实现36.90%,库存周转率为17.50%,产品不良率降低31.5%,产品研制周期缩短25%,运营成本降低37.26%,生产效率提升41.33%。2019年,入选国家智能制造标杆企业。
评论
加载更多